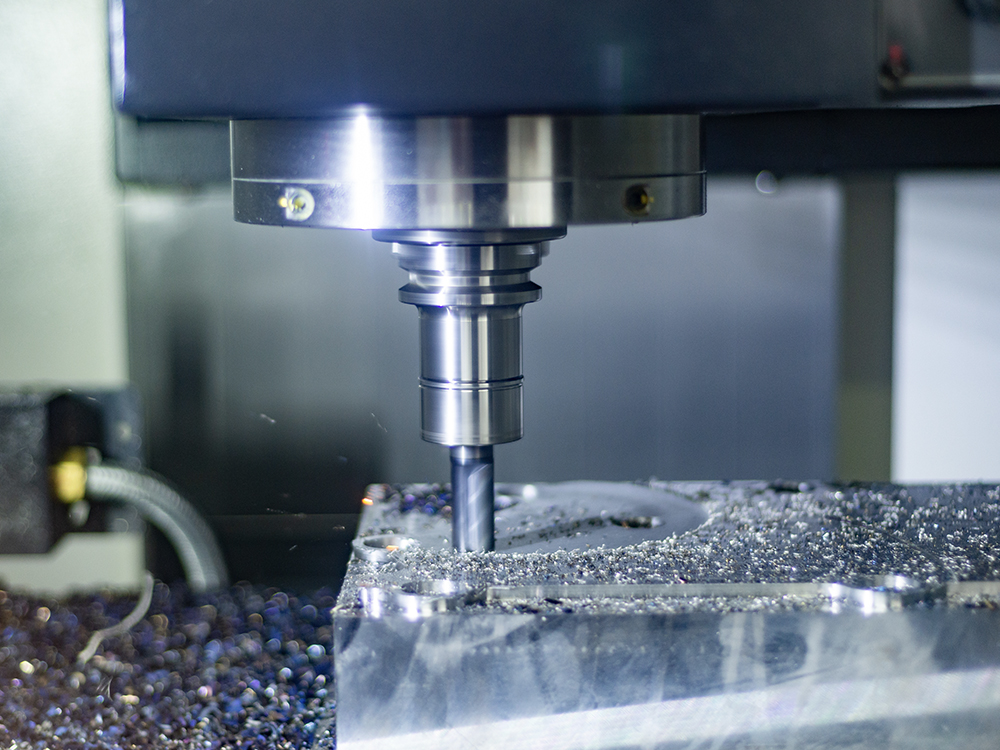
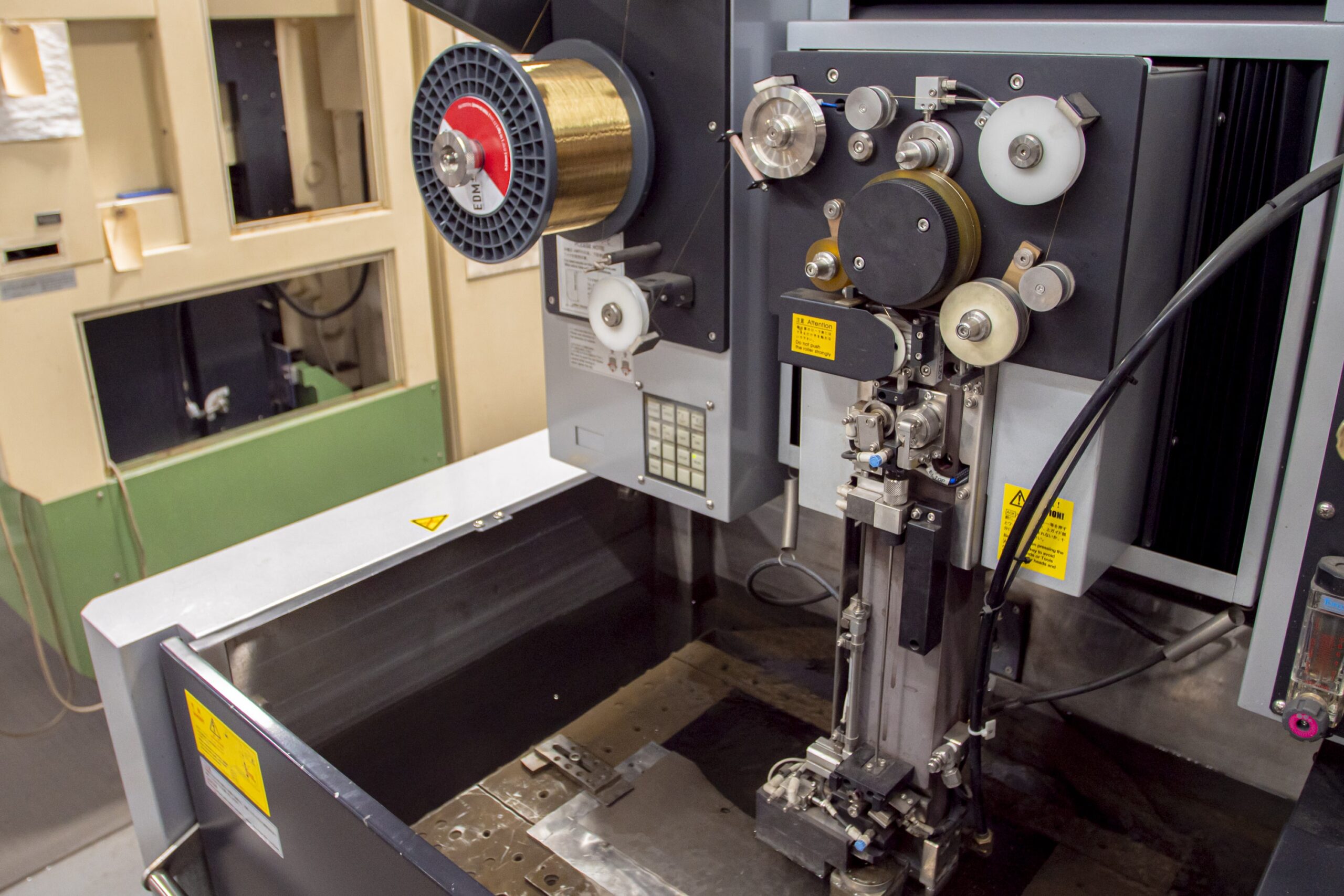
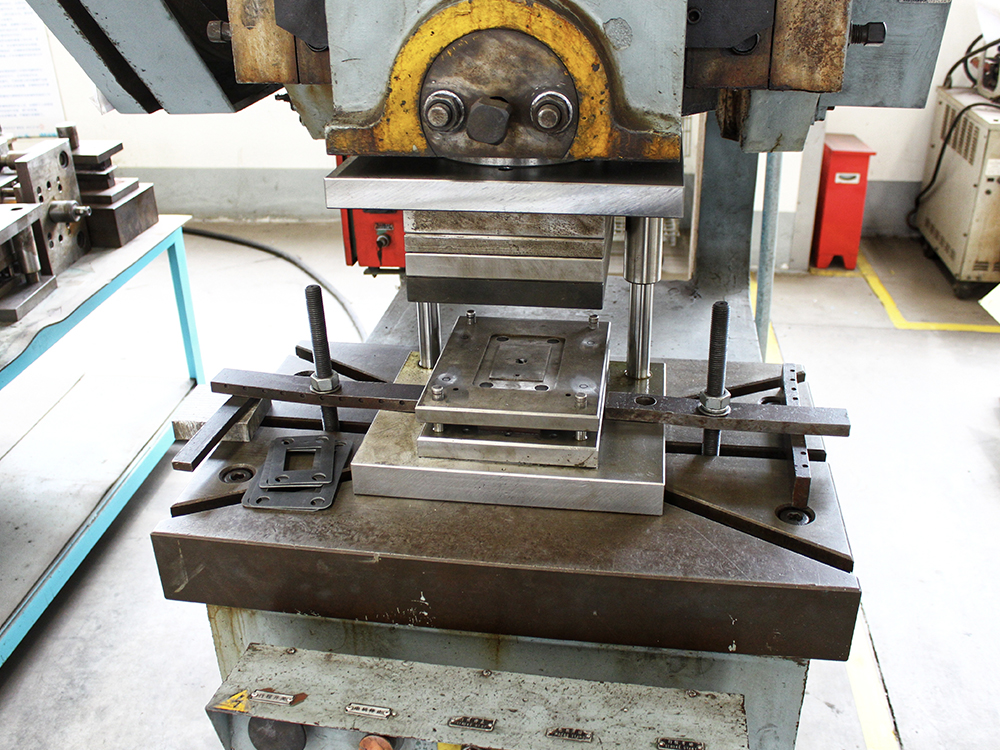
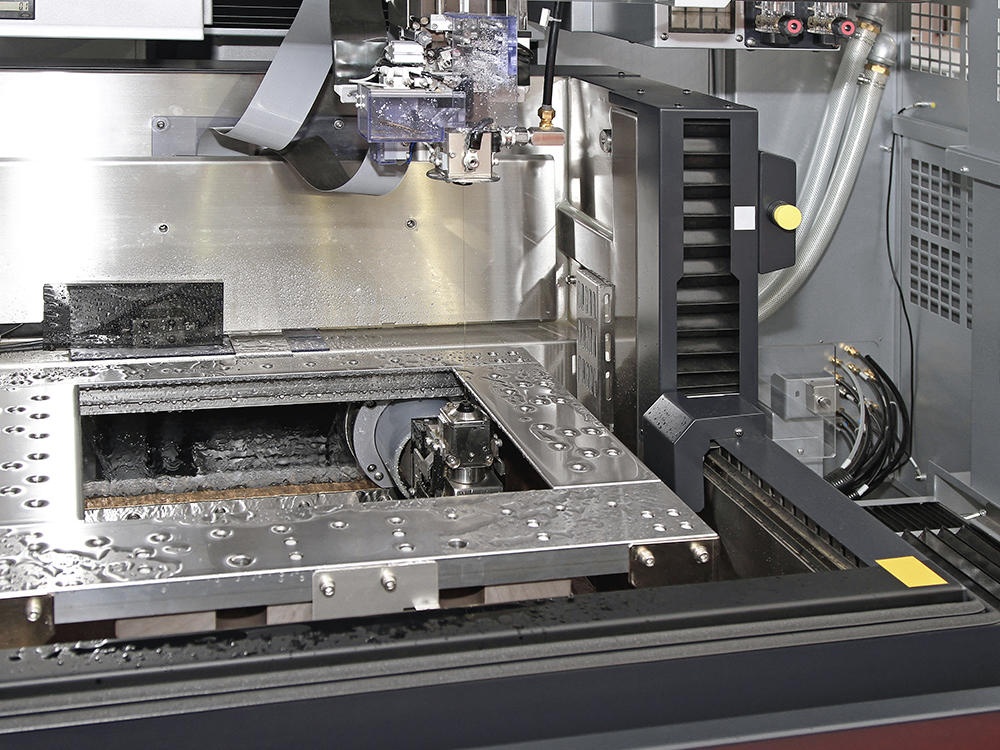
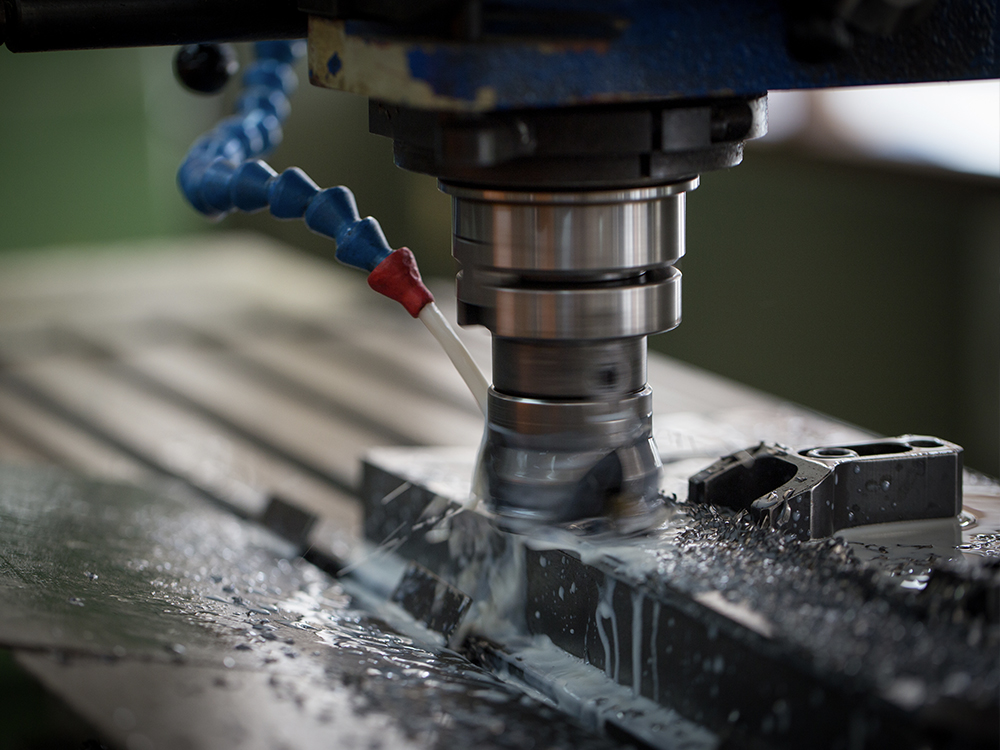
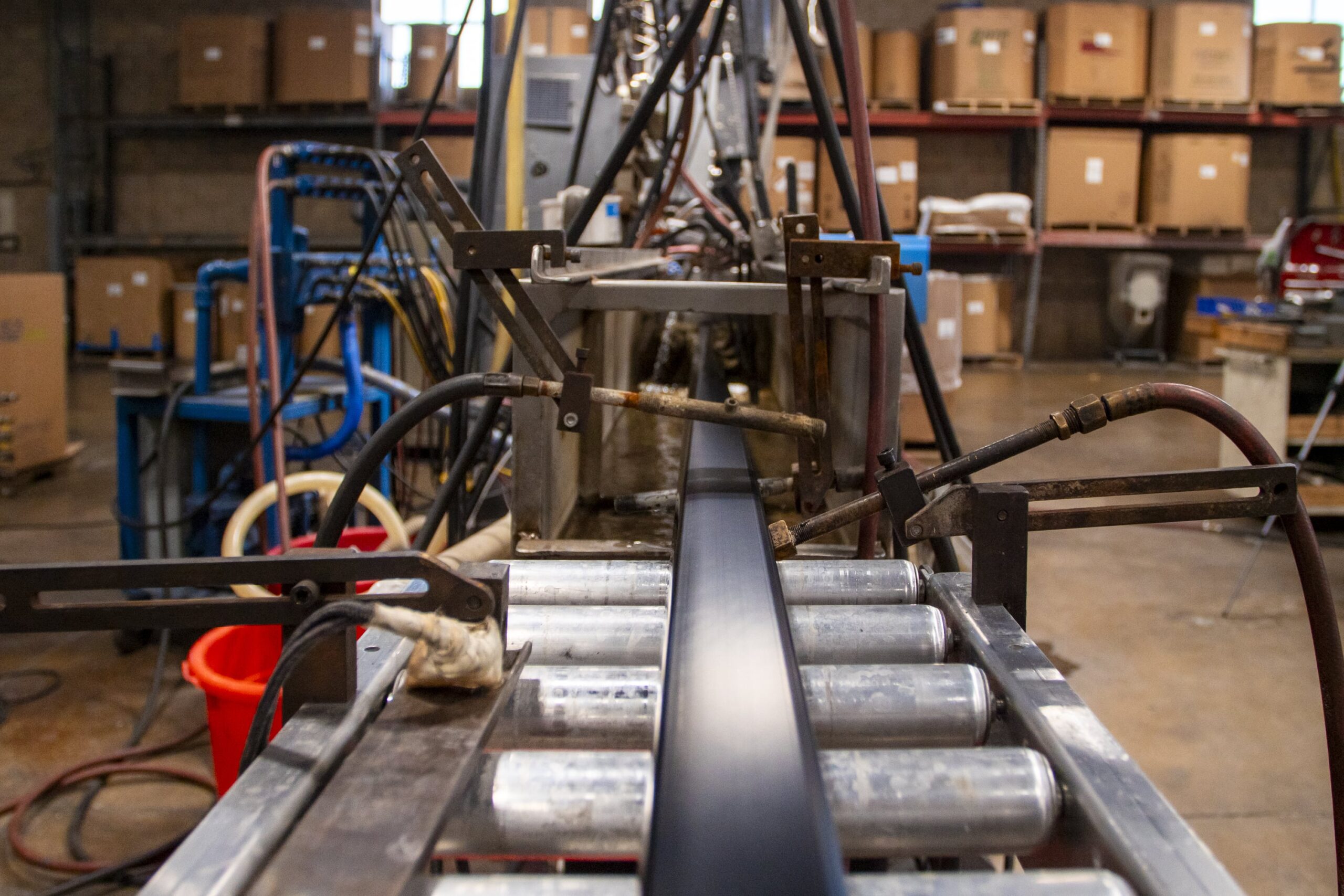
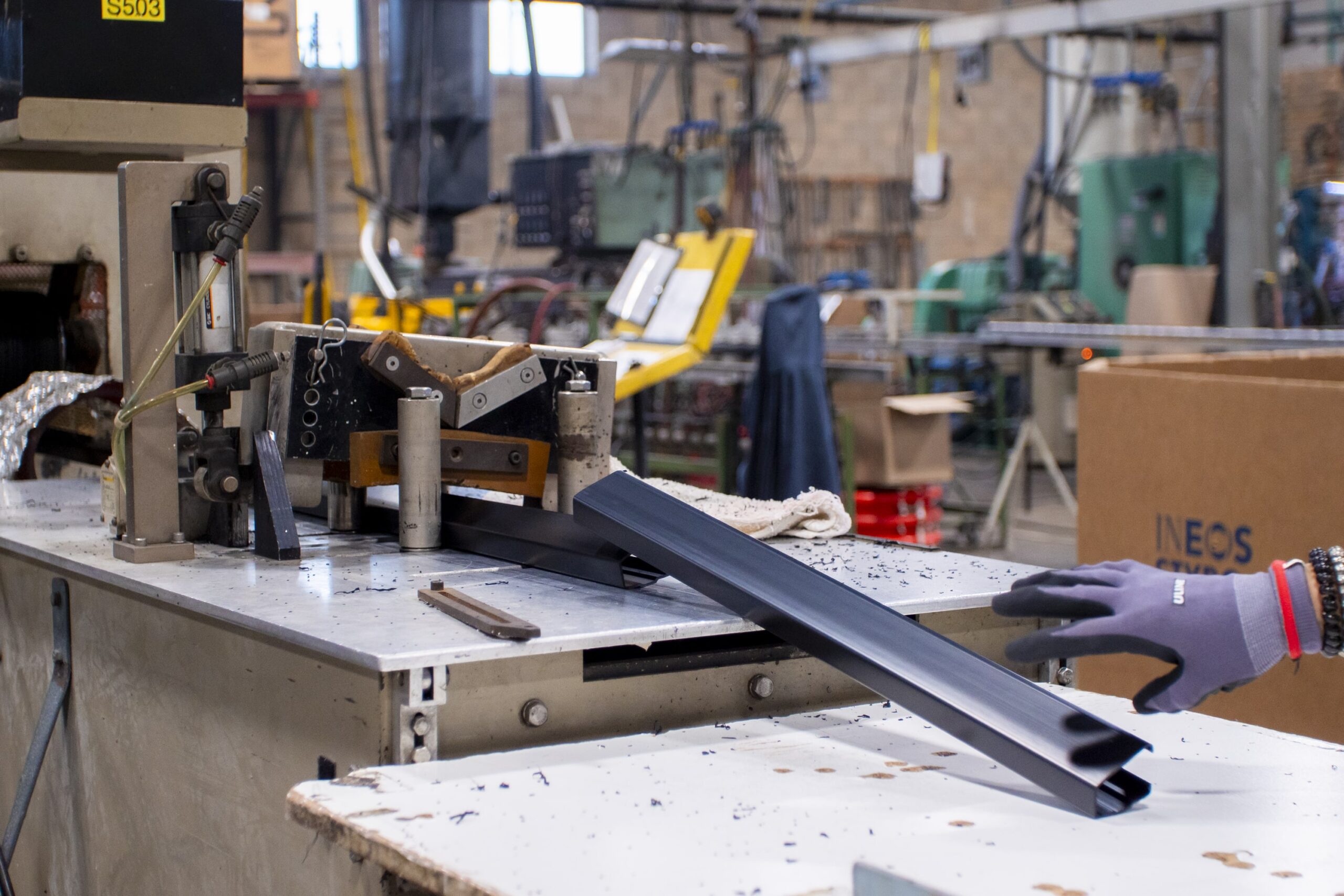
How Do You Make Plastic Extrusions?
Plastic extrusions are essential to many industries, helping products and components work reliably and efficiently. The process involves pushing raw plastic through a custom die to create long, continuous shapes with a consistent cross-section. These shapes are then used in various applications, from automotive parts to medical devices and consumer goods.
At E&C Custom Plastic Extrusion, we pride ourselves on being at the forefront of this technology. With years of expertise and a commitment to innovation, we provide tailored solutions that meet each industry's unique needs.
Whether you're seeking enhanced durability, specific shaping, or custom material formulations, our specialists are here to deliver exceptional quality and service.
What are Plastic Extrusions?
Plastic extrusions are versatile components used in many industries. But what exactly are they? Simply put, plastic extrusions involve shaping raw plastic materials into specific profiles. This process forms long, continuous shapes with a consistent cross-section.
Here's how it works. First, raw plastic material is fed into an extruder. The extruder heats the plastic until it melts. Then, the molten plastic is pushed through a custom die. This die molds the plastic into the desired shape. The result? Uniform plastic pieces that can be used in countless applications.
Why are plastic extrusions so popular? Their versatility makes them invaluable. In the automotive industry, they create durable parts. In healthcare, they become essential components of medical devices. Consumer goods also benefit from their use, incorporating them into everyday products.
At E&C Custom Plastic Extrusion, we understand the potential of plastic extrusions. Our technology allows us to meet any challenge. Need a specific shape? We can create it. Looking for durability? We know how to deliver.
Key Components of the Plastic Extrusion Process
Raw Materials
The type of plastic used in extrusion plays a crucial role. Common plastics include:
- polyethylene
- polypropylene
- PVC
Each type has unique properties. For instance, polyethylene is known for its flexibility and high-impact resistance. Polypropylene offers chemical resistance and toughness. PVC is valued for its rigidity and durability. At E&C Custom Plastic Extrusion, we select the best material for your needs.
Extruder Machine
The extruder machine is the heart of the process. It melts the plastic and shapes it.
- Raw plastic pellets are poured into the hopper
- The extruder heats these pellets until they melt
- A rotating screw pushes the molten plastic forward
This smooth, steady movement is vital to achieving uniformity.
Die Design
The die molds the plastic into a specific shape. Think of it as a cookie cutter. The die design is vital to achieving the desired profile. Expert die design ensures consistency and precision.
At E&C, we customize dies to meet your exact requirements. Whether you need intricate shapes or simple forms, we deliver.
Cooling and Sizing
Once shaped, the plastic must cool and set. Cooling solidifies the material, locking in the shape. We use water baths or air cooling systems for this step. Proper cooling prevents warping or defects.
Sizing ensures that each extrusion meets precise measurements. A well-cooled and correctly sized product is ready for use.
Cutting and Finishing
Finally, we cut the extrusions to the required lengths. Precision cutting ensures each piece meets exact measurements. Additional finishing processes are completed as needed to ensure the product is ready for use.
At E&C Custom Plastic Extrusion, we take pride in every step. From material preparation to finishing, our process guarantees high-quality results. Contact us to learn how we can help with your custom plastic extrusion needs.
Quality Control in Plastic Extrusions
Quality control is essential in the plastic extrusion process. Every stage of production is closely monitored to ensure the best products possible.
From the start, we inspect raw materials. Only high-grade plastic pellets are used, guaranteeing the finished product is solid and durable. During extrusion, we measure temperature and pressure. Consistent conditions yield consistent results.
Die design also undergoes rigorous checks. Each die is tested for precision, avoiding any issues in shaping the plastic. Cooling and sizing are critical steps, too. We make sure the plastic cools evenly, and proper sizing tools keep dimensions accurate.
Cutting and finishing have their own quality checks. Each piece is inspected for defects. Smooth edges and exact lengths are a must. Our team conducts thorough final inspections to maintain the high standards we set.
E&C Custom Plastic Extrusion aims for excellence, and our quality control measures affirm this. Trust us for reliable, high-quality plastic extrusions.
Contact us to learn more about our stringent quality control practices.
Variety of Plastic Extrusion Products
Plastic extrusion is incredibly versatile. At E&C Custom Plastic Extrusion, we create a wide range of products, including tubes, channels, seals, and custom profiles—all tailored to your needs.
Tubes: We make tubes of all sizes and materials, perfect for plumbing, medical devices, and protective coverings.
Channels: Ideal for construction, automotive, and window components. Our channels are strong and durable.
Seals: Essential for weatherproofing, noise reduction, and sealing gaps. We produce seals that ensure a perfect fit.
Custom Profiles: Unique shapes for unique applications. From industrial parts to consumer goods, we can design and fabricate it.
Advanced Technologies in Plastic Extrusion
Plastic extrusion technology is constantly evolving. At E&C Custom Plastic Extrusion, we stay ahead with the latest advancements. Our investment in cutting-edge equipment and techniques sets us apart.
Precision Equipment: We use state-of-the-art machines to ensure accuracy and consistency in every product. Advanced controls monitor temperature and pressure precisely.
Innovative Materials: Our team explores new materials and additives that help improve strength, flexibility, and durability.
Automation: Automation enhances efficiency and repeatability. It reduces errors and speeds up production times.
Sustainable Practices: We focus on eco-friendly processes and materials. Our aim is to minimize waste and promote recycling.
Our commitment to technology means better products for you. We pride ourselves on delivering high-quality plastic extrusions every time.
Environmental Sustainability in Plastic Extrusions
At E&C Custom Plastic Extrusion, we are committed to protecting the environment. Sustainability is at the heart of what we do, and we focus on eco-friendly practices to reduce our carbon footprint.
Recycling: We recycle plastic waste to conserve resources. Our advanced recycling systems ensure minimal waste. This helps to keep plastic out of landfills.
Waste Reduction: Efficiency is key to reducing waste. We use automation to minimize errors and scrap. Any leftover materials are repurposed.
Sustainable Materials: We stay updated with the latest in sustainable materials. Biodegradable and recycled plastics are integrated into our product lines. This ensures our offerings are as green as possible.
Our green initiatives set us apart. By choosing E&C Custom Plastic Extrusion, you contribute to a cleaner planet. Making sustainable choices has never been easier.
Benefits of Custom Plastic Extrusions
Custom plastic extrusions offer many advantages. They are perfect for those needing specialized solutions.
Cost-Effectiveness: Custom extrusions can reduce costs in the long run. Tailored parts mean less wastage and more efficient designs.
Design Flexibility: You can create exactly what you need. We cater to unique dimensions and shapes, proving invaluable for specific applications.
Tailored Solutions: Custom extrusions help meet your exact requirements. Whether in the medical, automotive, or construction industries, we provide the perfect fit.
Choosing custom plastic extrusions offers unmatched benefits. It’s a smart choice for businesses looking to innovate and save.
Choose E&C Custom Plastic Extrusion
The plastic extrusion process is a fascinating blend of science and art. It allows for the creation of versatile and durable products. We explored how custom extrusions can bring cost savings, design flexibility, and tailored solutions to various industries.
At E&C Custom Plastic Extrusion, we pride ourselves on our commitment to sustainability. From recycling and waste reduction to using sustainable materials, we make eco-friendly practices a core part of our operations.
If you're looking for high-quality custom plastic extrusion solutions, look no further. Our expertise and dedication to green initiatives set us apart. Contact us today to learn how we can assist with your next project and help you effortlessly make sustainable choices. You can also request a quote!