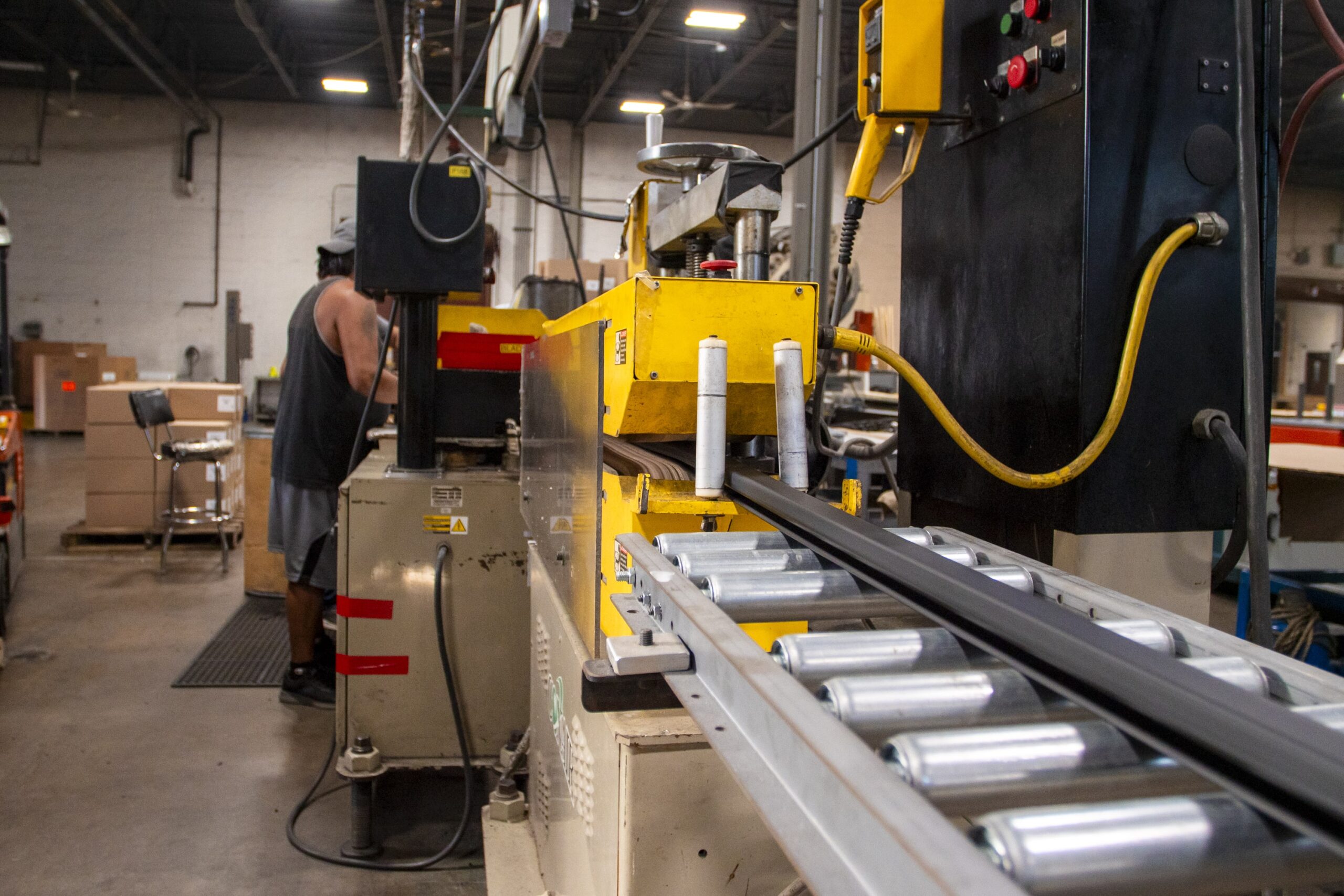
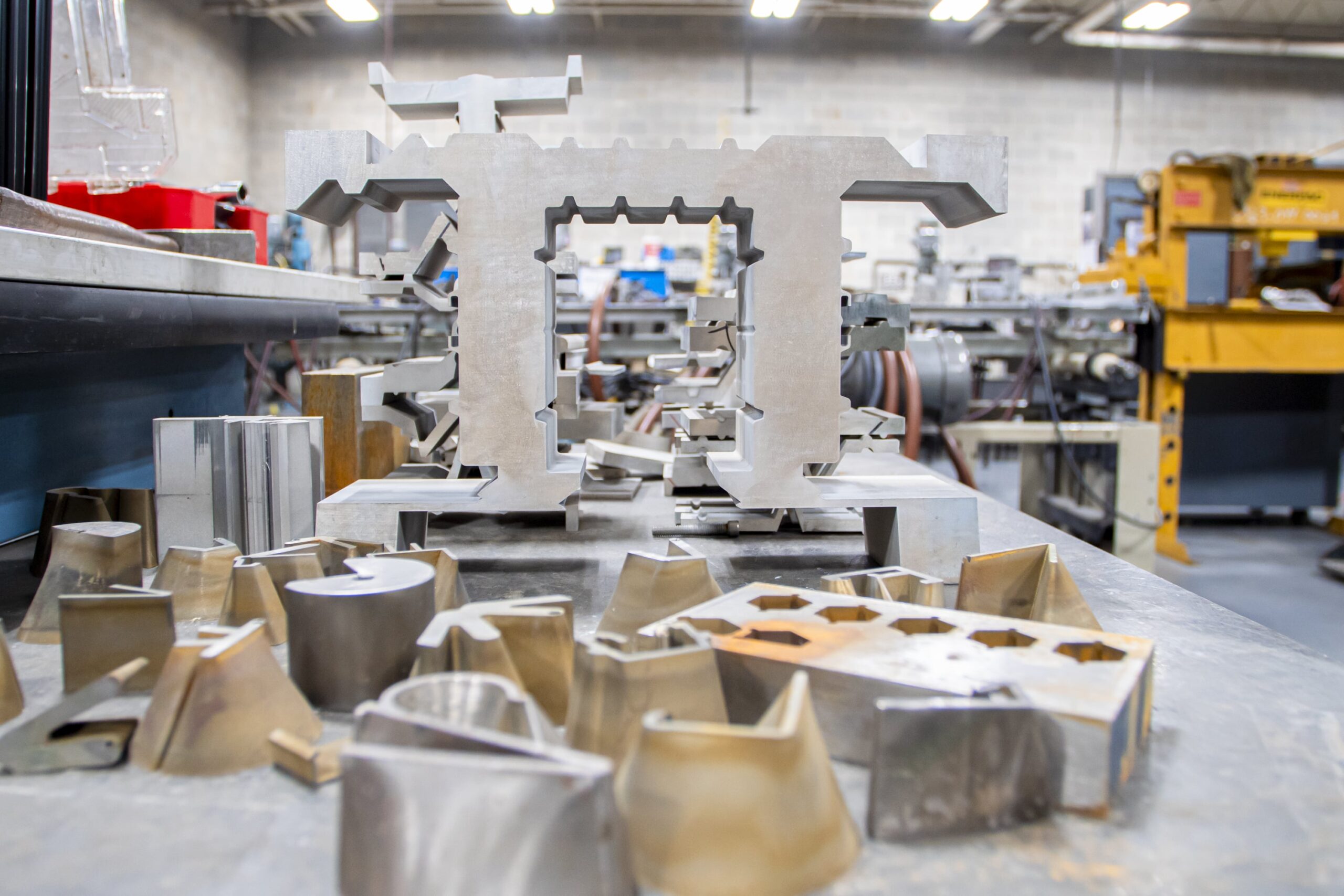
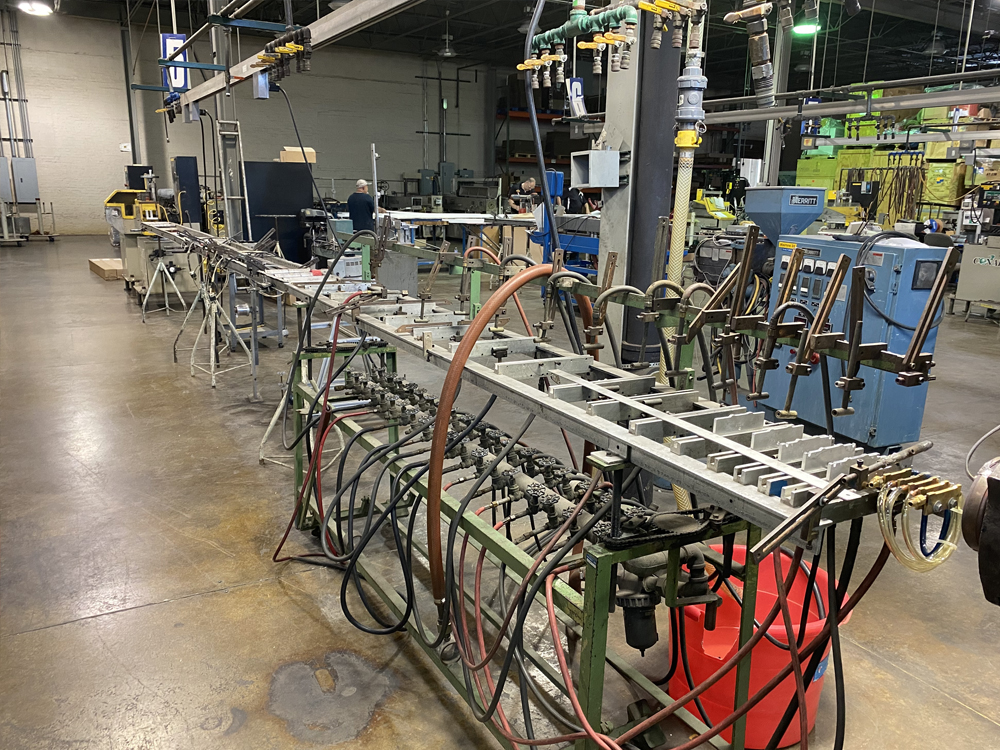
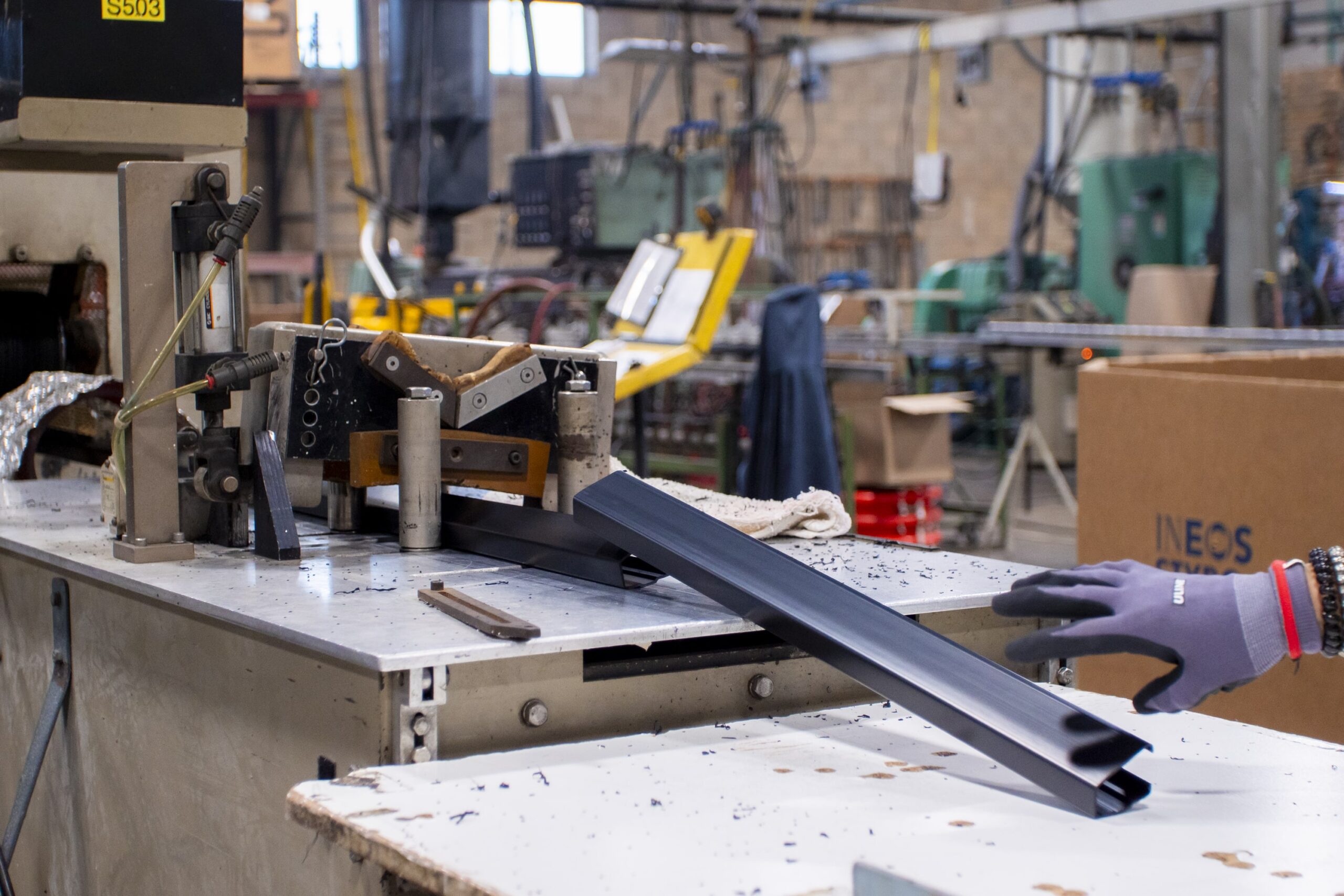
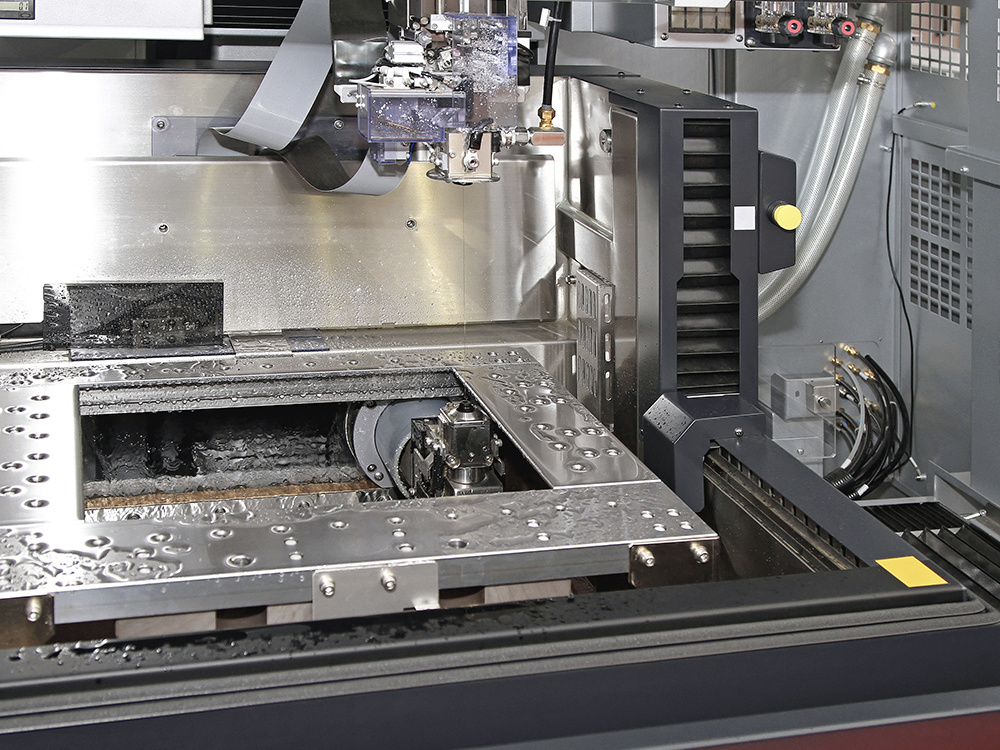
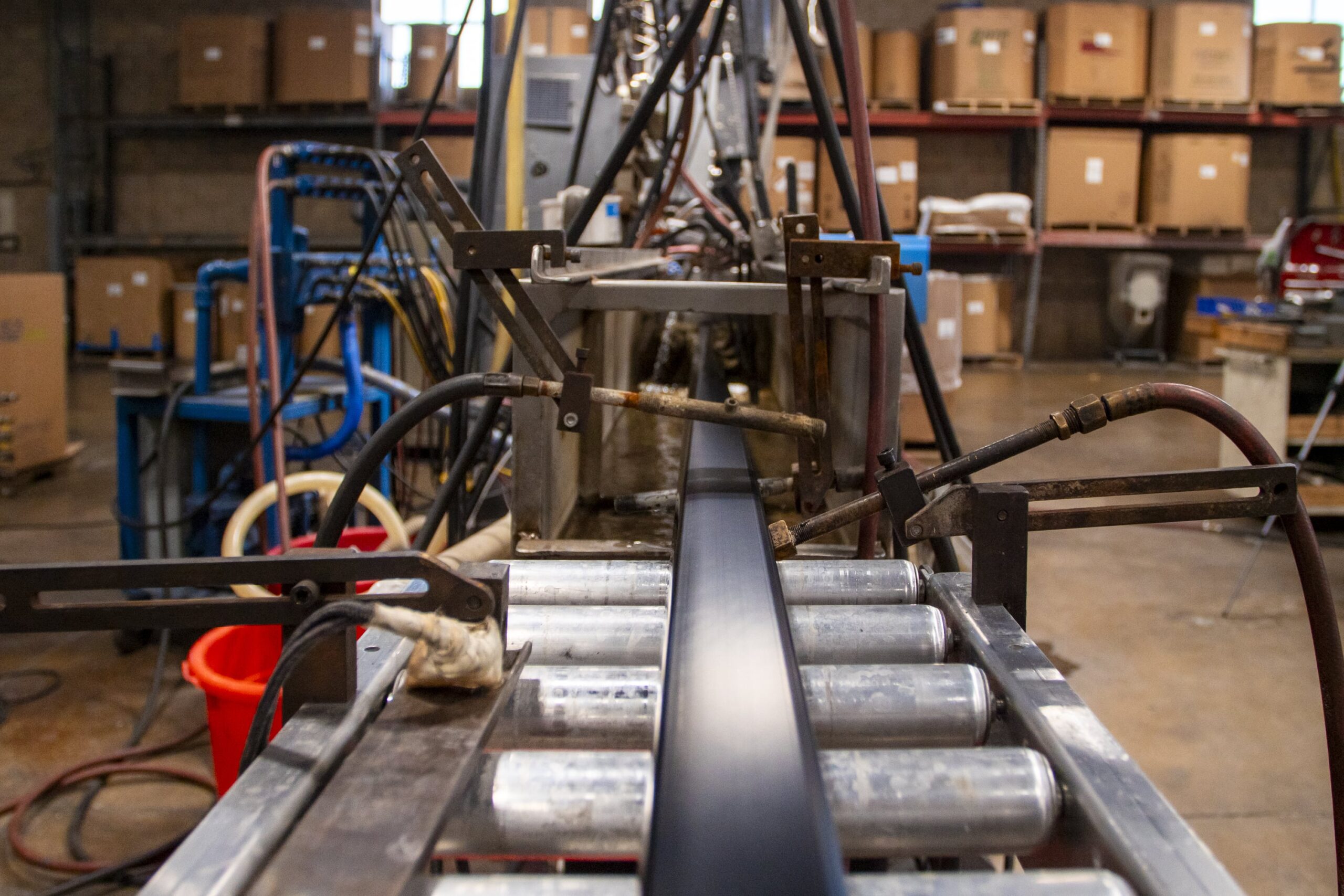
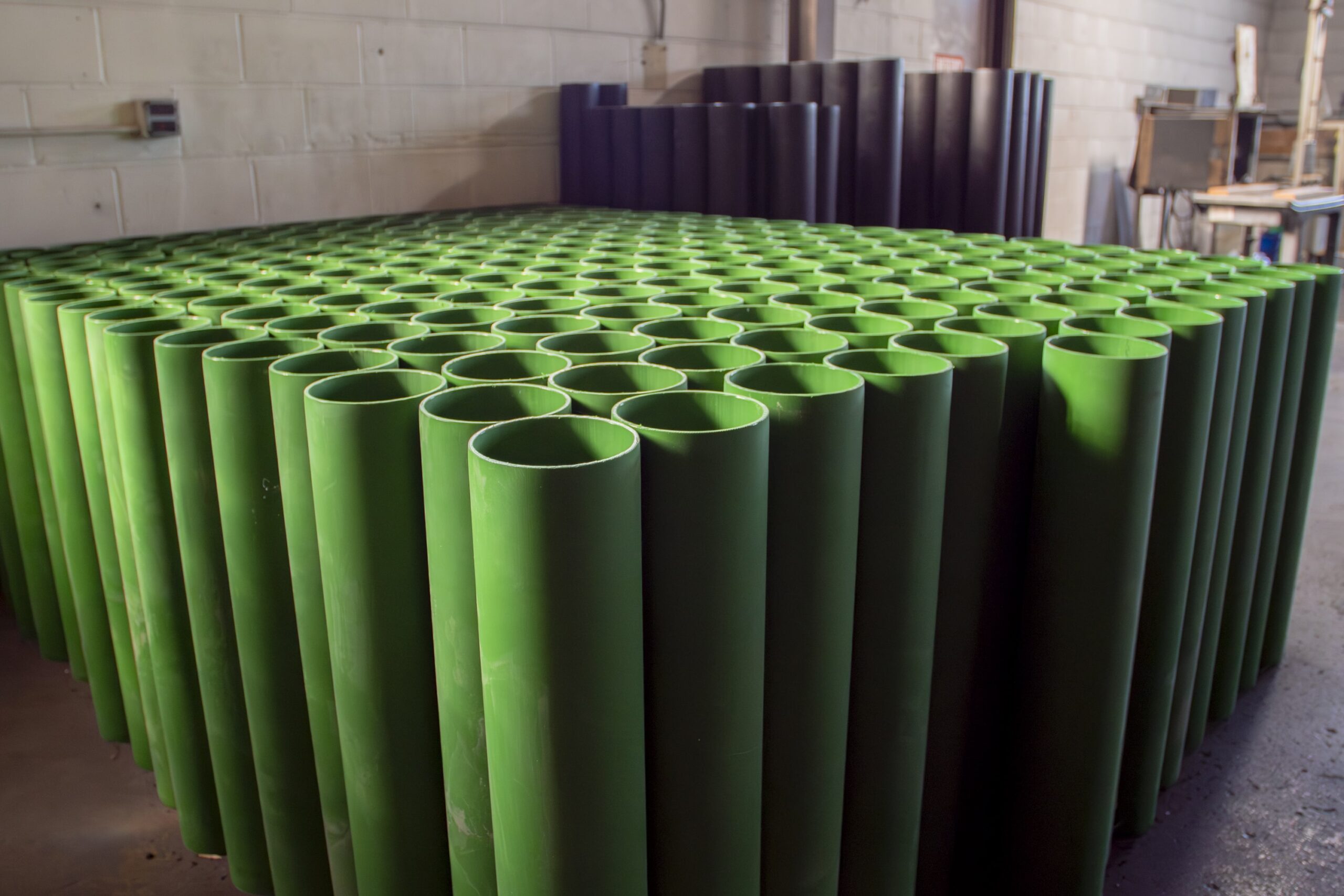
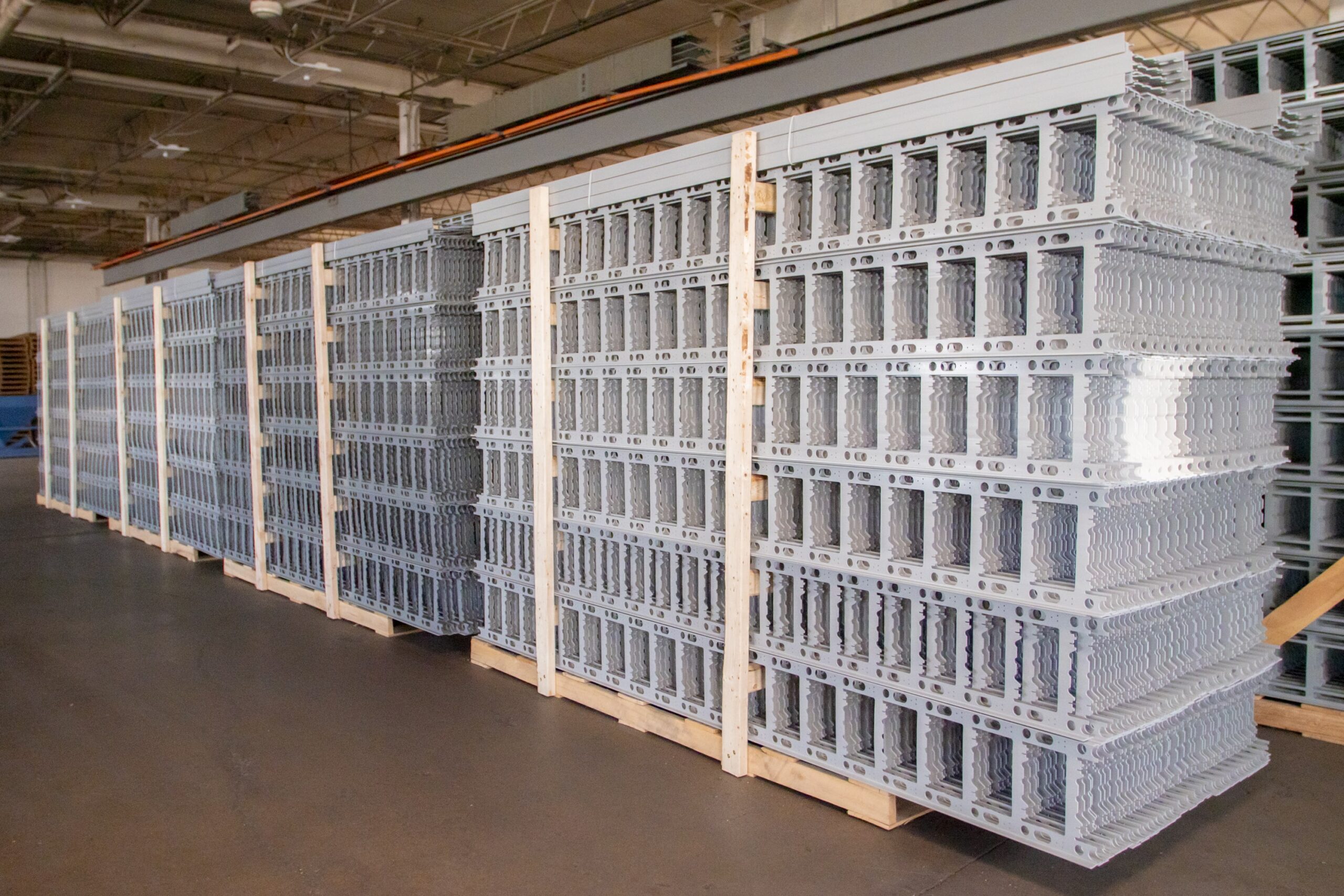
What are the True Costs of Plastic Extrusion?
Plastic extrusion is a popular manufacturing process that turns raw plastic materials into continuous profiles, such as pipes, sheets, and tubing. It's a versatile method used in various industries, from construction to automotive and consumer goods.
But when considering plastic extrusion for your business, one big question often comes to mind: "How much does it cost to extrude plastic?" Let's delve into this topic to understand the factors influencing these costs.
Answering the Question: How Much Does Plastic Extrusion Cost?
For simple profiles, costs can range from $0.50 to $2.50 per pound of plastic material. This is usually for straightforward shapes like pipes or basic sheets.
Costs can increase significantly if you're working with more complex custom designs. Intricate shapes, or projects requiring specialized materials, can cost anywhere from $5 to $10 per pound.
The volume also plays a crucial role. Larger orders benefit from economies of scale, lowering the per-unit cost. Small batch orders might not enjoy the same cost efficiency and may be more expensive per unit.
When planning your plastic extrusion project, consider these variables. They will help you estimate a realistic budget for your specific needs.
Factors Influencing the Cost of Plastic Extrusion
Material Costs
One of the biggest factors influencing the cost of plastic extrusion is the type and grade of plastic used. Common materials include PVC, HDPE, and ABS. Each material has a different price point and performance characteristics.
Higher-quality plastics generally cost more but offer better durability and performance. Additives and colorants can also affect the cost. These can improve properties like UV resistance or aesthetic appeal, but they add to the overall expense.
Design Complexity
The complexity of the die design used in extrusion significantly impacts costs. Simple, standard profiles are less expensive because they require less specialized engineering and machining.
On the other hand, intricate custom designs come with higher costs. These designs need advanced die-making skills and more production time, increasing the overall expense.
So, while a basic pipe may be relatively affordable, a custom-shaped profile could be much more expensive.
Production Volume
Production volume plays a key role in determining the cost of plastic extrusion. Larger production runs benefit from economies of scale, meaning the cost per unit goes down as the quantity increases. This is because the setup costs, which include labor and machine calibration, are spread over a larger number of units.
Smaller batches usually don't have this advantage, making each unit pricier. Therefore, larger orders can be more budget-friendly.
Machinery and Technology
Investment in advanced machinery and technology also influences costs. Modern, high-tech machines can be expensive but offer more efficient production and may save costs in the long run.
These machines can produce complex profiles with greater precision, reducing waste and speeding up production times. The initial investment might be high, but the benefits often outweigh the costs.
Labor and Overhead
Skilled labor is essential for plastic extrusion, and labor costs can vary. Operational overheads, including maintenance and energy consumption, also add to the overall cost.
Efficient production processes can help manage these expenses. Well-maintained machinery and trained operators can make the process smoother and more cost-effective.
Secondary Operations
Finally, secondary operations like cutting, finishing, packaging, and quality control add to the cost of plastic extrusion. These processes ensure the final product meets quality standards and customer requirements. Although they increase the total expense, they are crucial for delivering a high-quality product.
Comparative Cost Analysis: Plastic Extrusion vs. Other Methods
Cost is always a key factor in manufacturing. Let's compare plastic extrusion with other popular methods: injection molding, machining, and thermoforming.
Injection Molding is excellent for high-volume production runs. The initial setup cost is higher due to the cost of expensive molds. However, once set up, the price per unit drops significantly. This method excels in producing complex shapes but might not be cost-effective for smaller batches.
Machining involves cutting away material to create the final product. It's highly precise but can be costly due to the extensive labor and material waste. Machining is best for low-volume, high-precision parts but isn't typically suited for producing large quantities at a low cost.
Thermoforming heats a plastic sheet until it's pliable and then forms it over a mold. It's more affordable than injection molding for medium-sized production runs. However, it may have limitations with intricate designs and material usage.
Plastic Extrusion, on the other hand, offers a balanced cost-efficiency. It's ideal for producing long, continuous shapes and can efficiently handle high and low-volume runs. The initial setup costs are lower compared to injection molding, and it produces less waste than machining. Extrusion is often the most cost-effective for products like pipes, tubes, and profiles.
Each method has its strengths and ideal use cases. For high-volume, intricate parts, injection molding is a winner. For precision, machining takes the crown. For medium runs, thermoforming is a good choice.
However, plastic extrusion often provides the best value in terms of versatility and cost-effectiveness, especially for continuous shapes.
Strategies to Optimize Plastic Extrusion Costs
Optimizing costs in plastic extrusion is key to maintaining a competitive edge. Here are some strategies to consider:
Material Selection
Choosing the suitable material can significantly impact overall costs. Look for materials that provide the best balance of cost-efficiency and quality. For example, using recycled plastics can reduce costs while still maintaining durability. Always consult with your supplier to identify the most cost-effective options available.
Design for Manufacturability
Designing profiles that are easy to produce can save time and money. Keep the design simple by reducing complexity and avoiding intricate details. This not only speeds up the extrusion process but also decreases the chances of errors and material waste.
Batch Production
Larger production runs can significantly lower your per-unit costs. By taking advantage of economies of scale, you can spread the setup costs over larger units. This is especially beneficial if you have consistent demand or can store surplus products for future sales.
Process Efficiency
Efficient production planning is crucial. Optimize machine use and minimize downtime to boost productivity. Additionally, reducing material waste through careful planning and monitoring can further cut costs. Regular maintenance of equipment also ensures that production runs smoothly without unexpected halts.
By focusing on these strategies, you can make your plastic extrusion process more cost-effective while maintaining high-quality standards.
Value Beyond Initial Cost
Initial costs for plastic extrusion can seem daunting. However, the long-term benefits and value can far outweigh the upfront investment.
Durability and Performance
High-quality plastic extrusions are built to last. They endure harsh environments and heavy usage. This means fewer replacements and repairs. Over time, you save money and reduce downtime. Reliable products increase customer satisfaction and loyalty.
Customization
One size doesn't fit all. Tailored extrusion solutions cater to your specific needs. Custom designs can improve product functionality and performance. This flexibility allows you to innovate and differentiate from competitors. Meeting your exact requirements means better results and higher satisfaction.
Consistency
Consistent quality is crucial in mass production. It reduces defect rates and ensures product reliability. Customers appreciate reliable products that perform as expected. Fewer defects and returns translate to lower costs and happier clients. Consistency builds trust and enhances your brand reputation.
E&C Custom Plastic Extrusion's Cost-Effective Solutions
At E&C Custom Plastic Extrusion, we understand the importance of balancing cost and quality. Our solutions are designed to be competitive without compromising on excellence.
Expertise You Can Trust
Our team has decades of experience in the plastic extrusion industry. We know what it takes to deliver top-notch products. This expertise allows us to minimize waste and optimize production processes. The result? We pass on cost savings to you.
Advanced Technology
We invest in the latest technology for our extrusion processes. Advanced machinery ensures precision and efficiency. By automating key steps, we reduce human error and increase consistency. This level of technology means less rework and fewer defects.
Commitment to Value
Quality is our commitment. But we go beyond just delivering superior products. We aim to provide value at every stage of the process. Whether it's through custom designs or robust customer support, we focus on what matters to you. Our solutions are tailored to meet your needs, ensuring maximum efficiency and performance.
When you choose E&C Custom Plastic Extrusion, you're not just getting a product. You're investing in a partnership dedicated to your success.
Conclusion
In summary, we've covered the essentials of the cost of plastic extrusion. Let's recap the key points:
- Balancing Cost and Quality: At E&C Custom Plastic Extrusion, we ensure you get competitive pricing without compromising on quality.
- Expertise Matters: Our seasoned team minimizes waste and optimizes processes, passing cost savings to you.
- Advanced Technology: We use state-of-the-art machinery to enhance precision and efficiency, reducing errors and defects.
- Commitment to Value: Beyond quality, we focus on providing value through custom designs and robust customer support.
While costs can fluctuate based on factors like materials and complexity, plastic extrusion remains a cost-effective choice in many applications. It offers substantial value, especially when tailored to your specific needs.
Ready to experience the cost savings and superior quality of E&C Custom Plastic Extrusion? Contact us today for detailed quotes and customized solutions. Let us help you achieve maximum efficiency and performance.