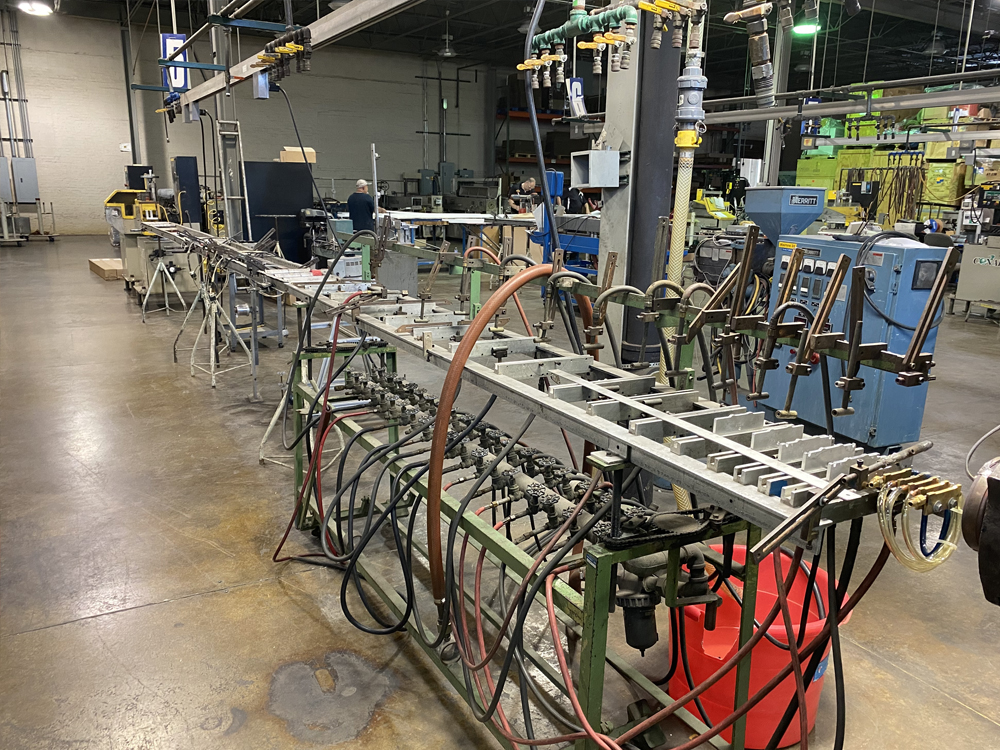
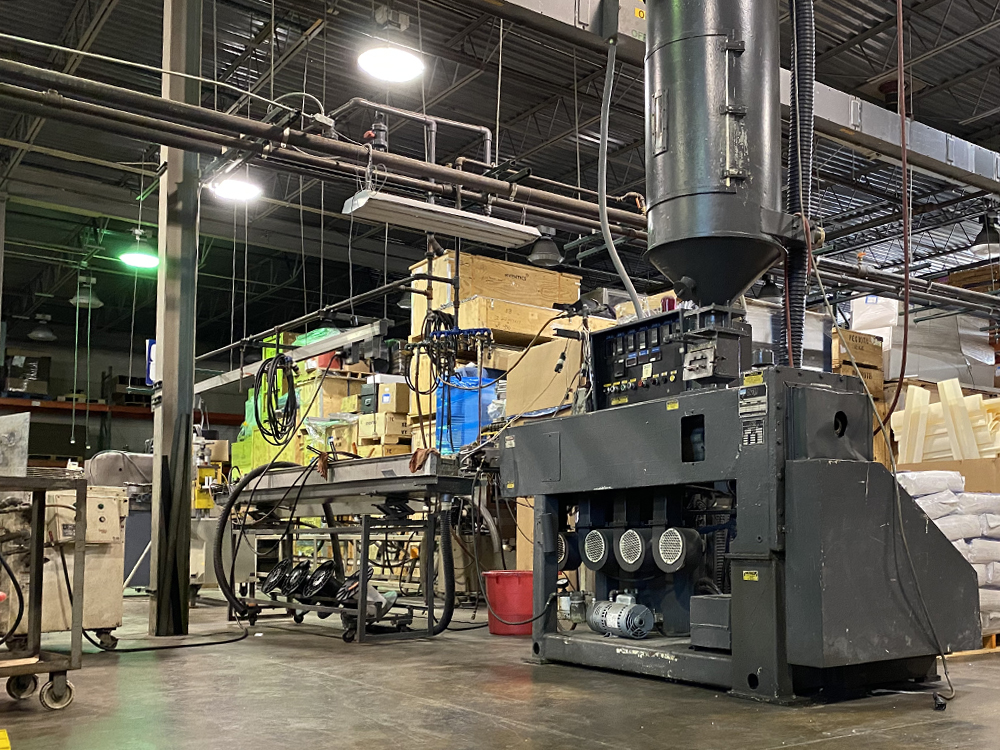
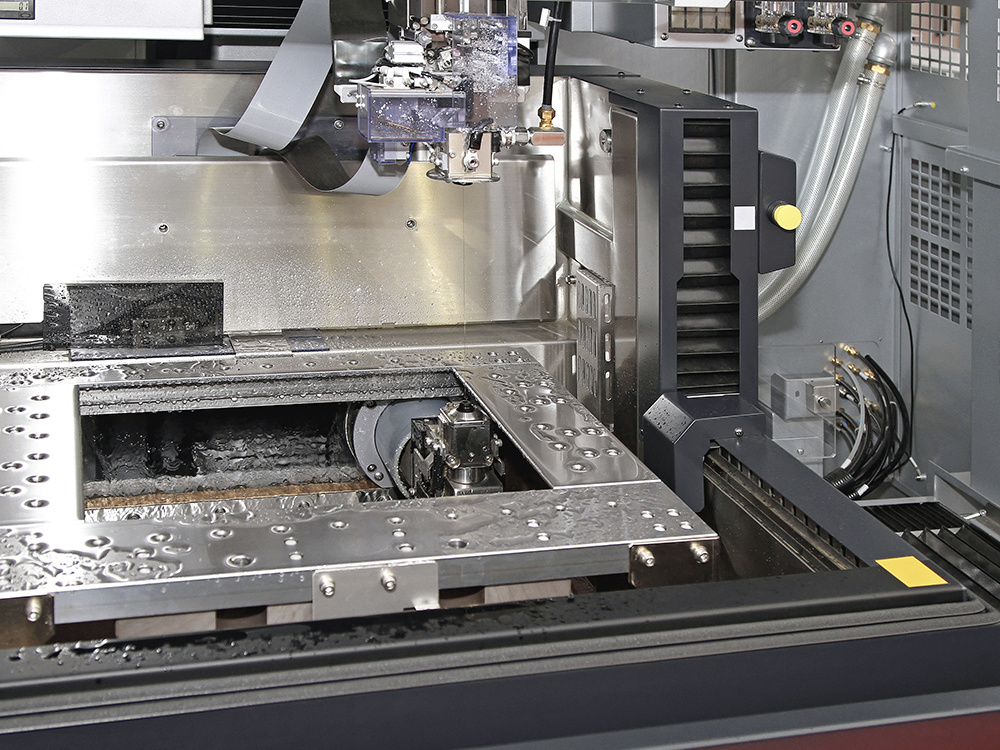
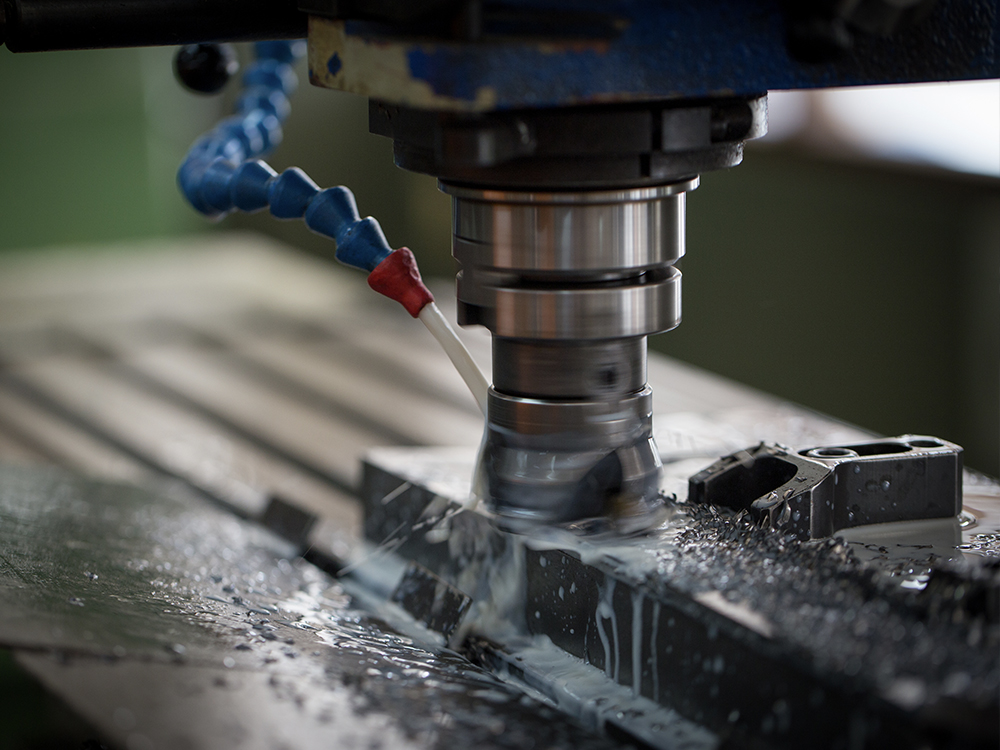
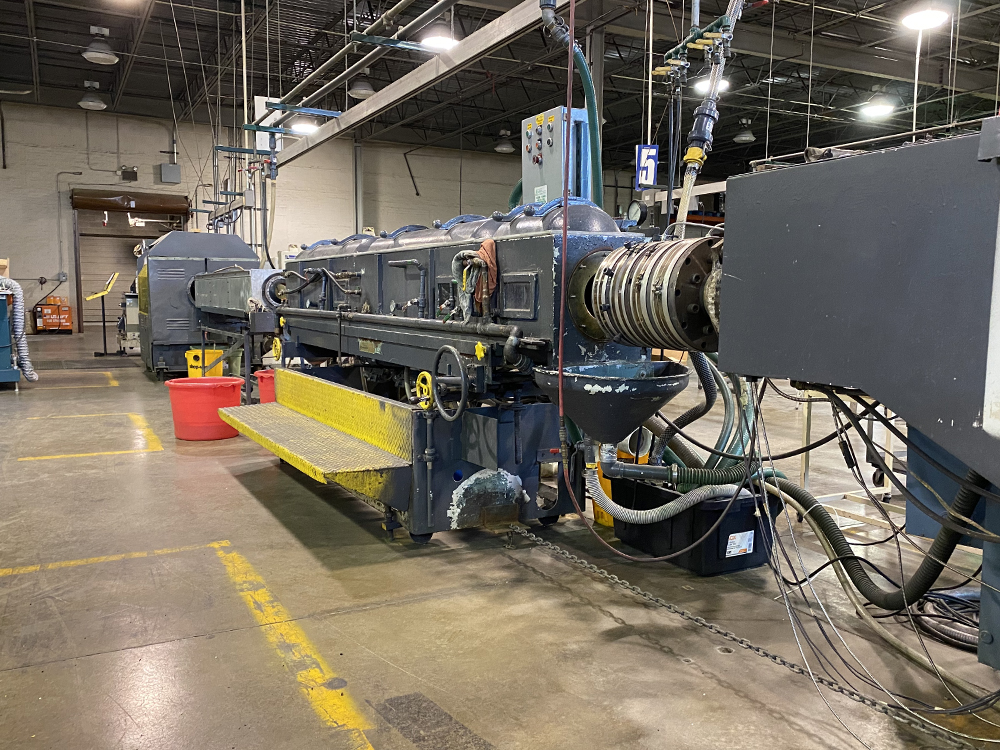
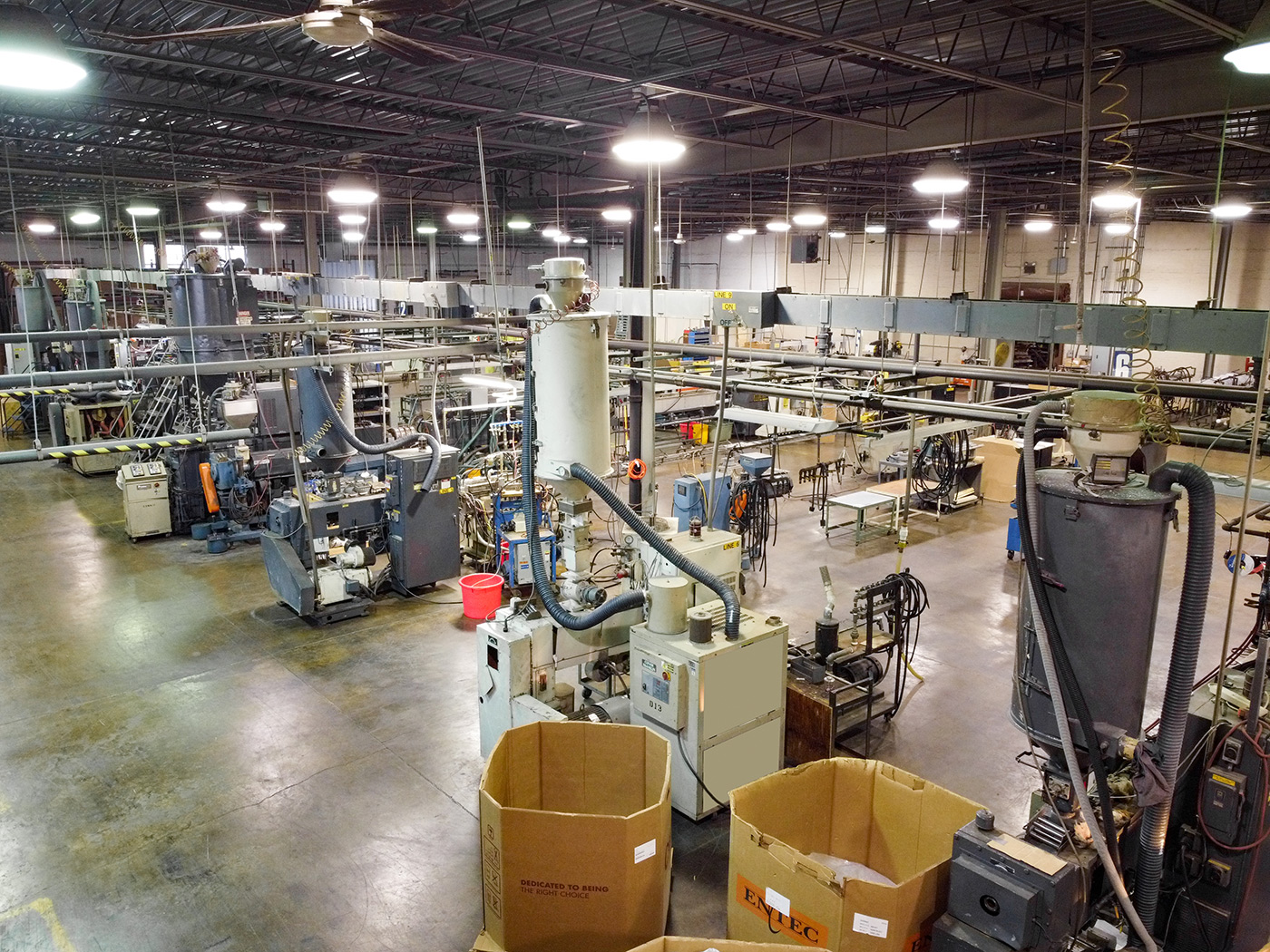
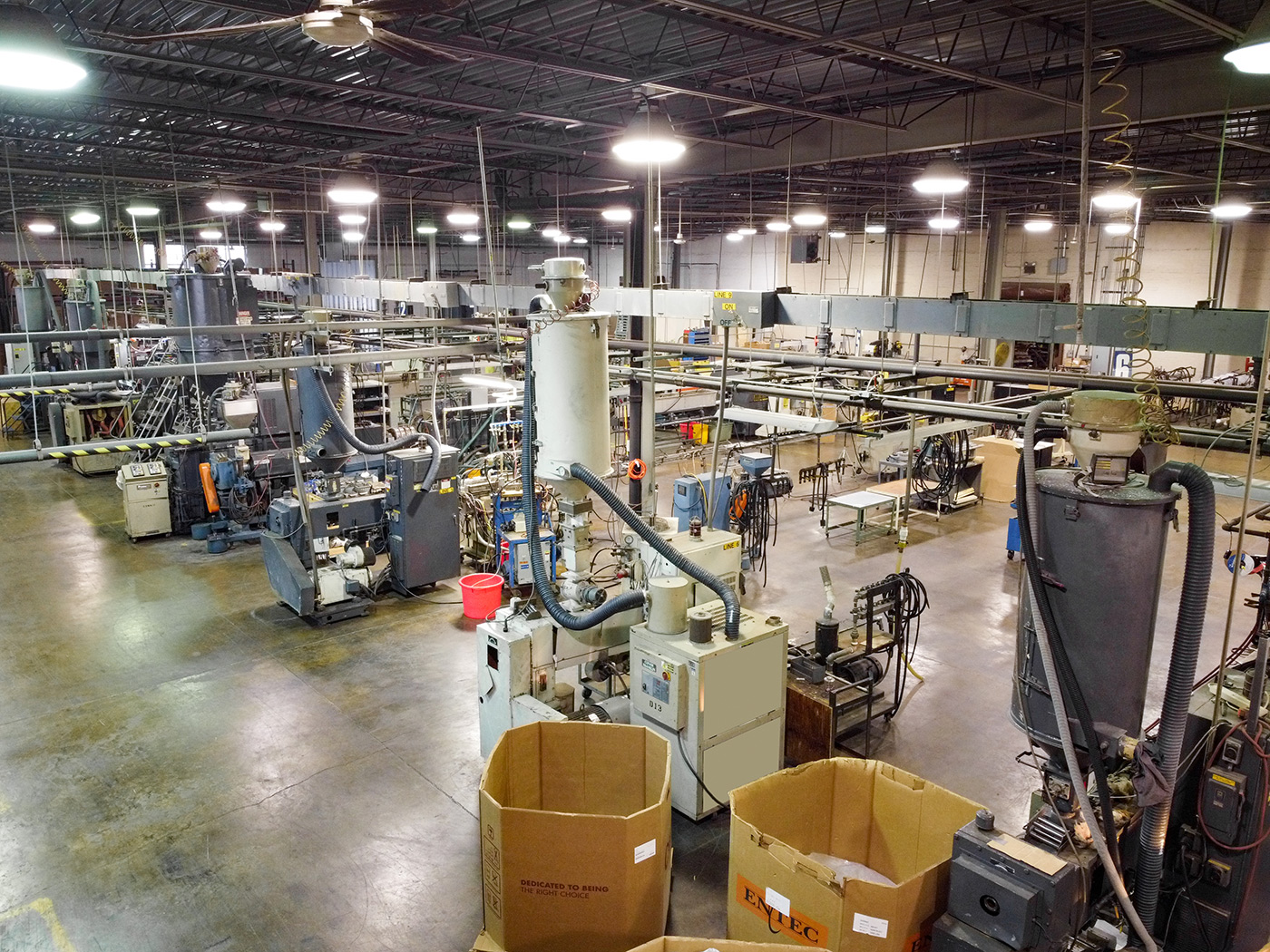

What is Plastic Extrusion Manufacturing?
Plastic extrusion manufacturing is an innovative process integral to many industries today. It plays a pivotal role in creating a myriad of products we use daily - from window frames and plastic films to tubing and pipes.
In this dynamic industrial era, the relevance of plastic extrusion manufacturing continues to grow, pushing the boundaries of product design and application.
E&C stands at the forefront of this technological revolution. We are proud industry leaders specializing in custom plastic extrusion manufacturing. With a relentless focus on quality, adaptability, and customer satisfaction, E&C strives to deliver solutions that meet and often exceed client expectations. Join us as we delve deeper into the fascinating world of plastic extrusion manufacturing.
Defining Plastic Extrusion Manufacturing
Plastic extrusion manufacturing is an efficient process where plastic material, in the form of pellets, is melted and continuously shaped into a profile. This high-volume manufacturing method is favored for its adaptability, enabling the creation of complex cross-sectional profiles tailored to various applications.
Tracing the Roots: History and Evolution of Plastic Extrusion Manufacturing
Extrusion as a process has its roots in the early 19th century, but it wasn't until the early 20th century that it found its way into the realm of plastics. The first plastic extrusion process created cellulose acetate items such as rods and pipes.
Over the years, the process has evolved, and technological advancements have enabled the creation of a diverse array of products.
Today, plastic extrusion manufacturing is a cornerstone process in industries ranging from construction and packaging to transportation and healthcare.
The Plastic Extrusion Process: A Step-by-Step Guide
The plastic extrusion process is both fascinating and complex, involving several crucial steps. Each of these steps contributes significantly to the quality and characteristics of the final product.
Step 1: Raw Material Selection
Everything begins with the right choice of raw material. The plastic pellets used should meet the performance and aesthetic requirements of the desired product. This choice dramatically impacts the product's durability, color, finish, and usage conditions.
Step 2: Drying the Plastic Pellets
The selected pellets are then dried. This step is critical because any moisture in the pellets can lead to defects in the final product. The drying process ensures that the pellets are in the perfect condition for extrusion.
Step 3: Melting the Pellets
The dried plastic pellets are then fed into the extruder, where they are heated and melted. The extruder is a crucial component, and its temperature settings matter significantly to the quality and properties of the final product.
Step 4: Shaping the Melted Plastic
The molten plastic is then pushed through a die, shaping it into a continuous profile. The die design is customized based on product specifications, allowing for the creation of a wide range of complex shapes.
Step 5: Cooling the Plastic
The hot, shaped plastic is then cooled. This step solidifies the plastic, allowing it to retain its shape. The cooling method varies depending on the plastic type and the product's size and shape.
Step 6: Cutting to Size
Finally, the cooled, solid plastic profile is cut to the desired length. The precision of this process ensures that every product is consistently the same size.
Each step of the plastic extrusion process is critical as it directly influences the final product's properties and performance. By understanding this process, we can appreciate the complexity and precision that goes into creating everyday items we often take for granted.
Types of Plastic Used in Extrusion
The plastic extrusion process utilizes various types of plastic, each having unique properties that make them suitable for specific applications. Understanding these materials is key to appreciating the versatility and potential of plastic extrusion.
Polyethylene (PE)
Polyethylene, or PE, is a common plastic used in extrusion due to its flexibility and durability. Its resistance to impact and moisture makes it ideal for creating products like plastic bags, bottles, and pipes.
Polypropylene (PP)
Polypropylene or PP is another commonly used plastic. It's renowned for its strength, elasticity, and resistance to high temperatures. These characteristics make PP perfect for creating automotive parts, containers, and medical equipment.
Polyvinyl Chloride (PVC)
PVC, or Polyvinyl Chloride, is a versatile plastic used in both rigid and flexible forms. Its high durability, cost-effectiveness, and resistance to environmental conditions make it suitable for applications like window frames, doors, and plumbing pipes.
Polystyrene (PS)
Polystyrene, or PS, is favored for its ease of molding and rigid nature. It's widely used in food packaging and insulation materials, as well as in creating disposable cutlery and plates.
Each of these plastics brings unique benefits to the table in the extrusion process, making them instrumental in the production of a vast array of items we use in our daily lives.
Applications of Plastic Extrusion Manufacturing
Plastic extrusion manufacturing is pivotal to numerous industries, with its applications spanning a vast range of products. The capability to mold plastics into complex shapes makes this technique an essential part of many manufacturing processes.
Packaging Industry
The packaging industry heavily relies on plastic extrusion manufacturing. It is used in creating plastic films and sheets for food packaging, bubble wraps for secure transportation, and plastic bags for retail. Polyethylene and Polypropylene are frequently used for their flexibility and strength.
Construction Industry
The construction industry also benefits greatly from plastic extrusion. Rigid plastics, like PVC, are used to produce window frames, doors, and plumbing pipes. This material is favored for its durability and resistance to environmental conditions.
Automotive Industry
Automotive parts such as bumpers, panels, and trims are also crafted through plastic extrusion. Polypropylene is commonly used in this sector due to its high-temperature resistance and strength.
Medical Industry
The medical industry uses plastic extrusion to create devices like intravenous (IV) tubes and bags. Polypropylene and Polyethylene are often used for these applications due to their durability and flexibility.
Advantages of Plastic Extrusion Manufacturing
Various industries embrace plastic extrusion manufacturing due to its iconic advantages. This process offers manufacturers cost-effective, versatile, and complex shape production solutions.
Cost-Effectiveness
One of the resounding advantages of plastic extrusion manufacturing is its economic efficiency. This manufacturing process allows for high-volume production at lower costs, which is particularly beneficial for industries like packaging and construction, where large-scale production is a daily norm.
For instance, the construction industry heavily relies on the cost-effectiveness of plastic extrusion manufacturing to mass-produce window frames, doors, and plumbing pipes affordably.
Versatility
Plastic extrusion manufacturing is renowned for its versatility. It can handle different types of plastic materials, including Polyethylene, Polypropylene, and PVC, making it a go-to manufacturing method across various industries.
The medical industry, for example, uses this versatile method to manufacture various medical devices such as intravenous (IV) tubes and bags.
Complex Shape Production
The ability of plastic extrusion manufacturing to produce complex shapes is another notable advantage. This feature becomes crucial when crafting intricate components like automotive parts, including bumpers, panels, and trims.
Leveraging this advantage, the automotive industry can efficiently produce complex car parts that meet the sector's stringent safety and quality standards.
Custom Plastic Extrusion at E&C
At E&C, we are at the forefront of catering to custom plastic extrusion needs, leveraging our cutting-edge technology and deep industry expertise.
Understanding Your Specific Needs
We start by comprehending your unique requirements. Whether it's a specific type of plastic material, a unique shape, or a high-volume production need, our team is committed to understanding the nuances of your project.
Designing your Custom Solution
Once we thoroughly understand your needs, our team of skilled engineers and designers begins to craft a custom-designed solution. We employ state-of-the-art software and tools to ensure precision and accuracy in every design.
Quality Assurance
At E&C, we don't compromise on quality. Every custom plastic extrusion we produce undergoes a stringent quality assurance process. We ensure that your product meets your specifications and adheres to the highest industry standards.
Timely Delivery
We comprehend the importance of time in your operations. That's why we work diligently to ensure your custom plastic extrusions are delivered on time. Our commitment to efficiency and accuracy ensures you can keep your projects moving without any hiccups.
Post-Production Support
Our relationship with you doesn't end with the delivery of your order. We offer post-production support to assist you with any questions or issues you may have. At E&C, your satisfaction is our ultimate goal.
Future Trends in Plastic Extrusion Manufacturing
As technology continues to evolve, so does the field of plastic extrusion manufacturing. One trend taking the industry by storm is the adoption of automation. This not only improves efficiency and accuracy but also enables manufacturers to easily meet high-volume demands.
Furthermore, the emergence of biodegradable plastics and recycled materials is revolutionizing the industry, offering sustainable solutions that minimize environmental impact. The innovation of 3D printing technology also enables the creation of complex, custom shapes, meeting the specific needs of diverse sectors.
Staying Ahead with E&C
At E&C, we're not just observing these trends. We're actively incorporating them into our processes. Our commitment to embracing innovation ensures that we stay ahead of the curve, offering our clients the best service possible.
We're investing in automated systems to boost our efficiency and precision. Additionally, we're exploring the use of sustainable materials in our extrusion processes, working towards our commitment to a greener planet.
With E&C, you're not just getting a service provider. You're partnering with a forward-thinking leader in plastic extrusion manufacturing.
Interested in learning more about our services or discussing a project? Don't hesitate to contact us. Our team is eager to assist you and answer all your inquiries.
If you're ready to take the next step, you can request a quote directly on our website. Partner with E&C and benefit from our innovative approach to plastic extrusion manufacturing.