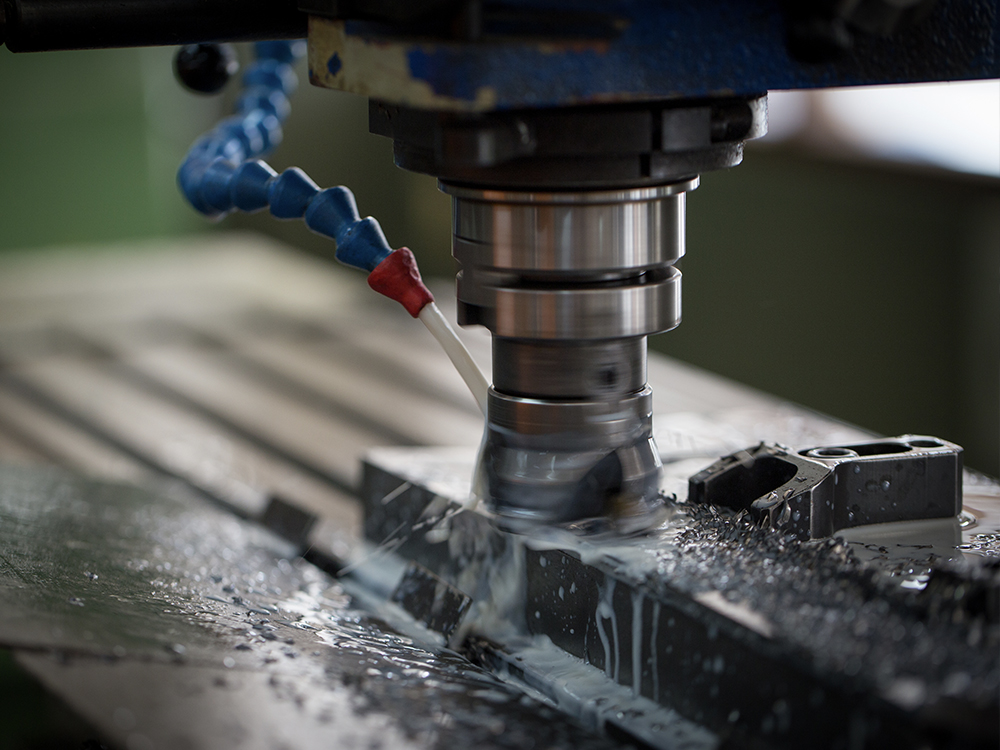
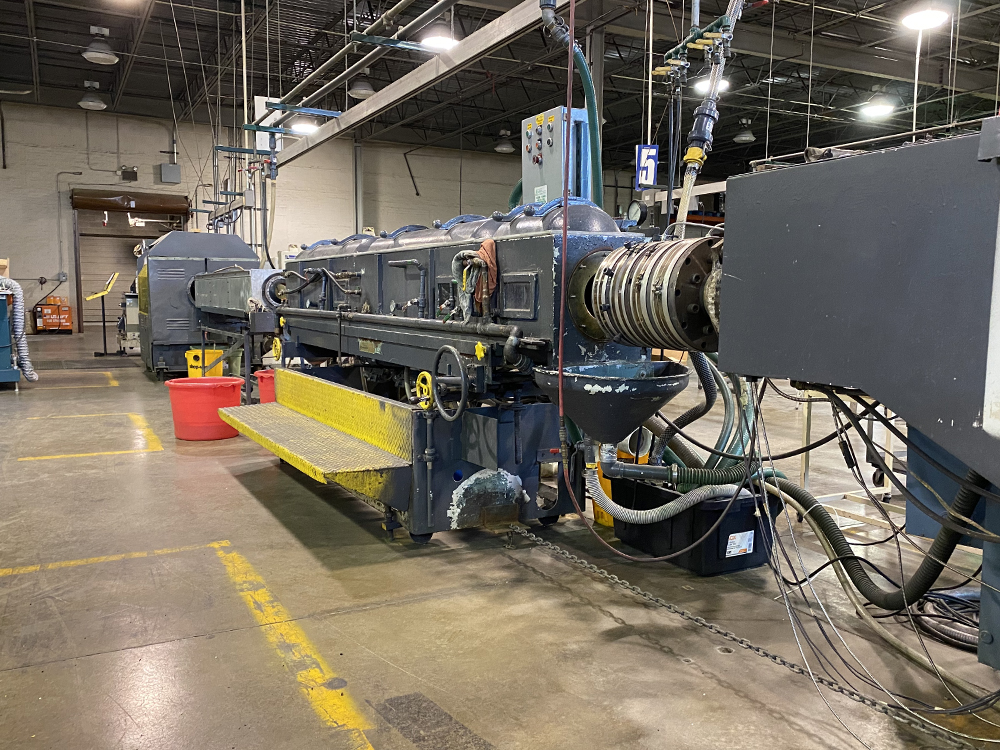
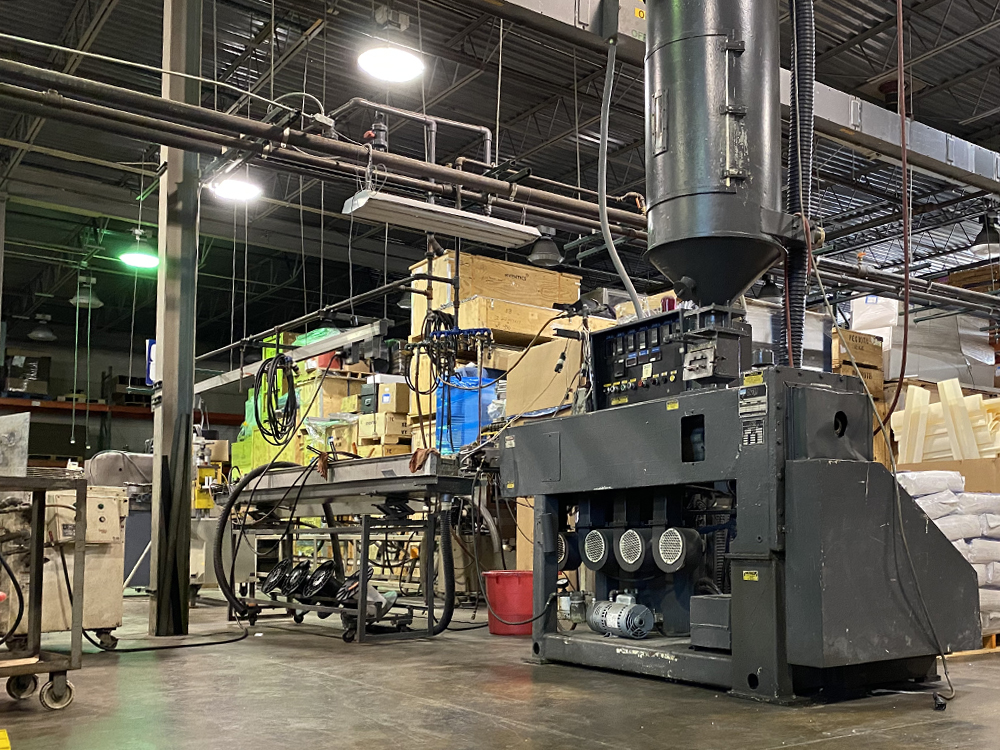

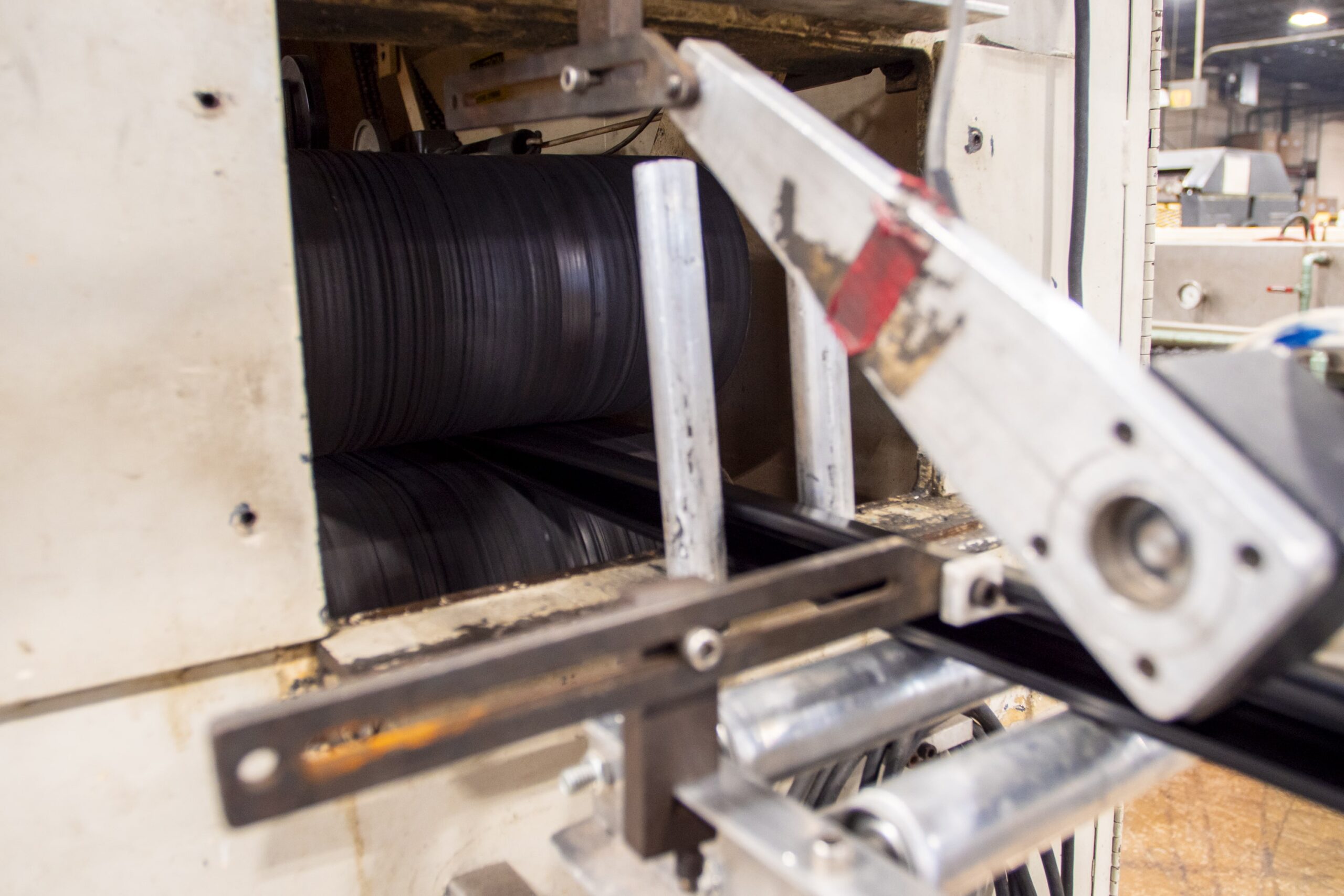
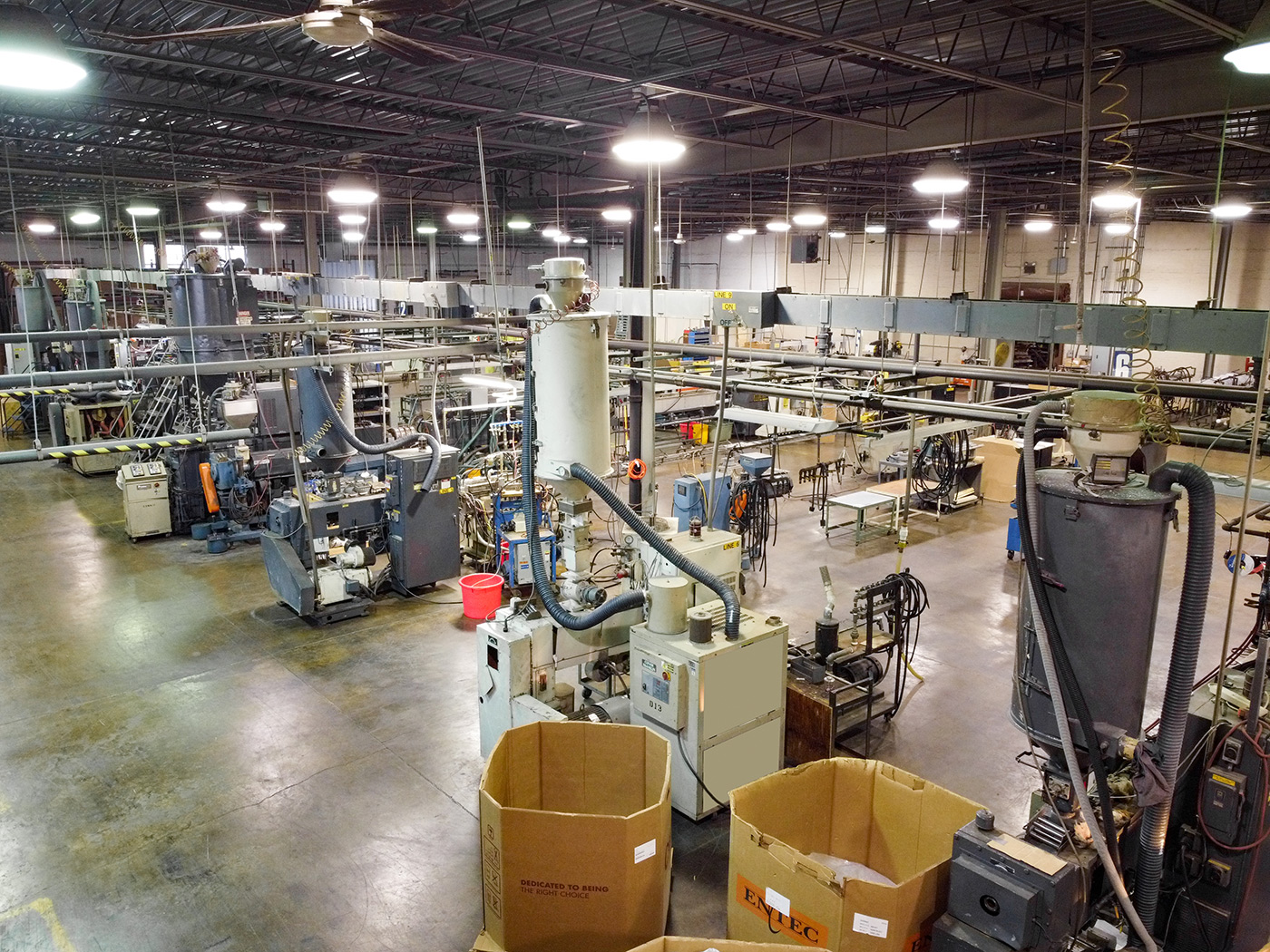
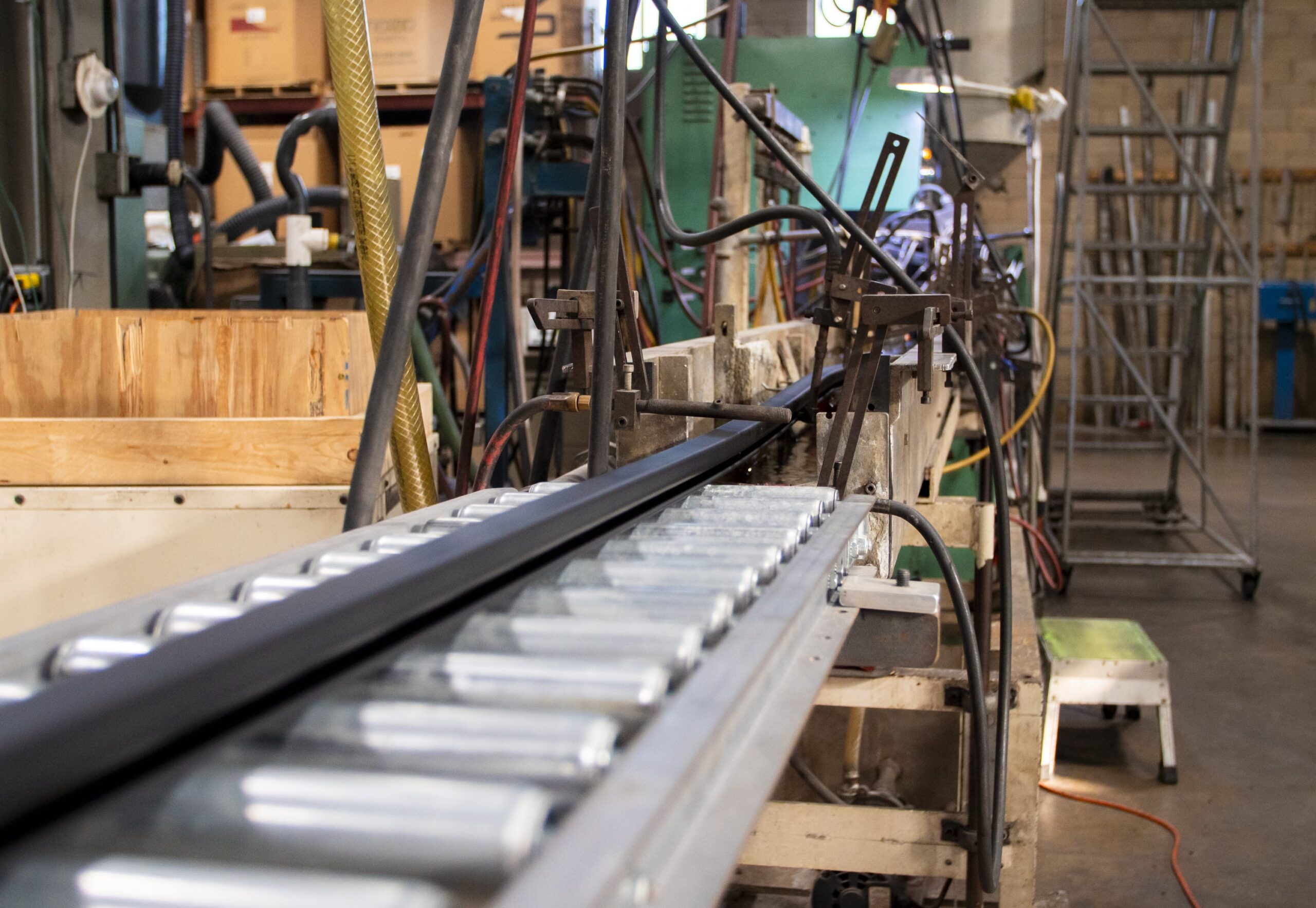
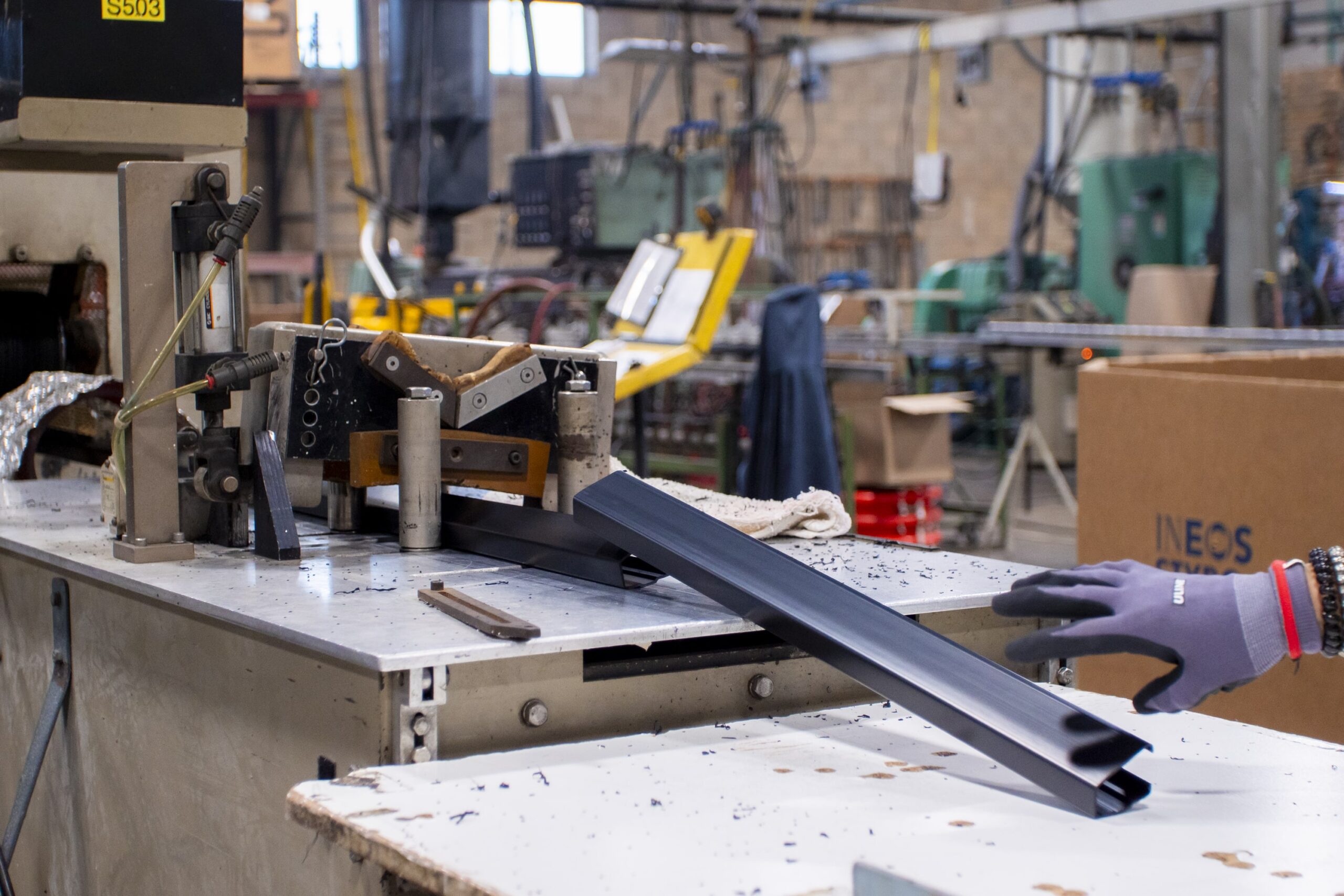
What is the Largest Plastic Extruder?
Welcome on board with E&C, your leading partner for custom plastic extrusion. We are excited to take you on a journey through the world of plastic extrusion and provide you with insights into the industry.
In this section, we will focus on one of the most crucial aspects of plastic extrusion: size.
What is Plastic Extrusion?
Plastic extrusion is a sophisticated manufacturing process that melts raw plastic and forms it into a continuous profile. It's a significant process in various industries, including automotive, construction, and packaging. Why? Because it allows for mass production of plastic components with consistent quality.
The Giant in the Room: The World's Largest Plastic Extruder
Let's shift focus to the titan of plastic extrusion - the world's largest plastic extruder. It's a game-changer worth exploring. Its sheer size allows for increased production capacities, making it a key player in meeting the high demands of various industries. Stay tuned to learn more.
The Basics of Plastic Extrusion: Turning Raw Materials into Versatile Products
Plastic extrusion is a high-volume manufacturing process that transforms raw plastic into a continuous, uniform profile.
This process involves melting plastic materials and forcing them through a die- a tool that shapes the plastic into profiles with a specific cross-sectional shape. As the plastic comes out of the die, it is cooled and hardened into the desired shape, ready for countless applications.
The Versatility of Plastic Extrusion: A Spectrum of Applications
The versatility of plastic extrusion is unrivaled. It forms the backbone of numerous industries, including construction, where it's used to create piping, wire insulation, and window frames.
The automotive industry utilizes it for manufacturing parts like weather stripping and trim. Even the medical industry relies on extrusion for creating tubing, seals, and more.
This versatility stems from the ability to shape plastic into infinite forms, making it an indispensable process across industries.
Extrusion: The Heart of Manufacturing Processes
Discussion of manufacturing could only be completed by recognizing the critical role of extrusion. Its ability to create consistent, high-quality output while maximizing raw material usage is invaluable. As a result, it significantly reduces waste, thereby promoting cost-effectiveness and sustainability in manufacturing processes.
It's no wonder industries around the globe consider extrusion an essential part of their operations.
Understanding the Size and Capacity of Plastic Extruders
In the world of plastic extrusion, the size and capacity of an extruder play vital roles. These factors determine not just the scale of production but also the final product's quality and characteristics.
Concept of Size and Capacity
The size of an extruder typically refers to the diameter of its screw, measured in inches or millimeters. Meanwhile, capacity usually refers to the amount of plastic a machine can process within a given period, often quantified in pounds or kilograms per hour.
Factors Determining the Size of an Extruder
Several factors influence the size of an extruder. One key factor is throughput, the rate at which plastic can be processed, which directly correlates with the extruder's capacity. The larger the extruder, the higher the throughput and, thus, the greater the capacity.
Another factor is the die size- the tool that shapes the plastic. Larger die sizes require larger extruders to generate the necessary pressure to force the plastic through the die.
Commonly Used Extruder Sizes in the Industry
Extruder sizes commonly used in the industry vary widely, accommodating a vast range of manufacturing needs.
For instance, smaller extruders, such as those with a 1.5-inch diameter, are perfect for creating thin, delicate profiles like medical tubing. On the other hand, larger extruders with diameters up to 6 inches or more are capable of producing substantial profiles like piping for construction purposes.
It's this incredible versatility that makes plastic extrusion such a prevalent manufacturing process across various industries.
Unveiling the Largest Plastic Extruder
Stepping into the titan realm of plastic extrusion, we introduce the largest plastic extruder currently known in the industry. This phenomenal machine boasts an unprecedented screw diameter of 12 inches, dwarfing its counterparts and enabling it to work with a staggering volume of plastic.
Incredible Size and Capacity
The sheer physical size of this extruder is a sight to behold. But what truly sets it apart is its extraordinary capacity. This mammoth machine can process thousands of pounds of plastic per hour, a testament to its unparalleled processing power.
The highest throughput levels, unseen in the industry until now, are effortlessly achieved by this groundbreaking machine.
Notable Capabilities and Achievements
The capabilities of the largest extruder extend far beyond its size and capacity. It has been a game-changer in the industry, facilitating the production of massive plastic profiles that were previously unthinkable.
This giant has been instrumental in accomplishing some of the most ambitious projects in the sector, including large-scale construction projects and extensive piping systems.
It's this unprecedented capacity and capability that truly cement the largest plastic extruder's status as a remarkable industry achiever.
Applications of the Largest Plastic Extruder
The largest plastic extruder is not just a testament to engineering prowess; it holds practical applications that are reshaping numerous industries. Here are some of the sectors where this extruder shines:
Construction Industry
In the construction sector, the extruder is playing a pivotal role in creating large-scale infrastructure. It has enabled the manufacture of oversized plastic elements for building structures, significantly reducing construction time, costs, and environmental impact. Buildings that have utilized this technology are not only sturdier but also more sustainable.
Automotive Manufacturing
The automotive industry has also greatly benefited from the largest plastic extruder. It is particularly useful in producing large, lightweight plastic components, improving the overall efficiency and fuel economy of vehicles without compromising safety or functionality.
Success Stories
A variety of companies have successfully utilized the largest extruder to spearhead innovative projects and create unprecedented products. One notable example is a leading construction company that used the extruder to produce large-diameter plastic pipes for a massive aqueduct project.
The pipes' durability and longevity, made possible through the extruder's capabilities, ensured a safe and efficient water supply for the surrounding communities.
Another success story involves a prestigious automotive manufacturer that leveraged the extruder's capacity to produce lightweight vehicle parts. These parts not only enhanced fuel efficiency but also met stringent safety standards, ensuring a win-win solution for both the manufacturer and the consumers.
In these ways, the largest plastic extruder continues to revolutionize industries, pushing the boundaries of what is possible in plastic manufacturing.
Technological Advancements
In recent years, the field of plastic extrusion has witnessed significant technological advancements that have enabled the development of larger and more efficient extruders.
One such advancement is the integration of AI and machine learning in the plastic extrusion process. This allows for real-time monitoring and adjustments during the production process, resulting in:
- enhanced precision
- reduced waste
- improved product consistency
Additionally, advancements in material science have led to the creation of high-performance plastics that retain their structural integrity even when extruded into larger shapes and sizes.
Future Possibilities
Looking ahead, the future of plastic extrusion appears bright and promising, thanks to the rapid pace of technological innovation.
There is potential for the development of hybrid extruders that combine multiple manufacturing processes into a single machine, resulting in unprecedented levels of efficiency and flexibility.
We may also witness the rise of biodegradable plastics and green manufacturing practices, which would greatly reduce the environmental impact of plastic production. This aligns with the growing global emphasis on sustainability and could revolutionize the plastic industry as a whole.
As such, the continued exploration of these possibilities will undoubtedly lead to even greater capabilities in plastic extrusion.
Key Takeaways
In summary, the exciting field of plastic extrusion is experiencing exponential growth due to recent and significant technological advancements. These include the integration of Artificial Intelligence and machine learning for improved precision, waste reduction, and better product consistency.
We also discussed the advent of high-performance plastics, the potential development of hybrid extruders, and the promising future of biodegradable plastics and green manufacturing practices that align with global sustainability goals.
Importance of Largest Plastic Extruder
The largest plastic extruder is a game-changer - it provides the capacity to meet robust industry demands, allowing for mass production with minimal waste and ultra-high precision. This technological marvel is instrumental in driving innovation and efficiency, directly benefiting the plastic extrusion industry.
Let's Explore E&C's Custom Plastic Extrusion Services
At E&C, we understand that every need is unique. Therefore, we offer a range of custom plastic extrusion services that can be tailored to suit your specific requirements. If you're looking to tap into the immense potential of plastic extrusion, look no further.
We invite you to contact us or request a quote today. Let's explore how E&C can help you achieve your production goals and exceed your expectations.